工廠生產力提升的關鍵:選擇最佳生產管理系統
工廠的生產力提升,選擇最佳生產管理系統是關鍵。採用雲端原生系統能帶來靈活性和擴充套件性,例如你可以隨時隨地監控生產狀況,不再受限於實體裝置。這對於應對突發狀況相當有幫助。整合人工智慧和機器學習技術,可以讓決策自動化,比如資源分配、生產排程等繁瑣工作都能交給AI處理,大幅提高效率。匯入可客製化儀錶板,你能即時看到裝置效能、生產率等重要資料,有問題馬上就能發現並且解決。不需要高深的專業知識,只需簡單設定,就能大幅提升工廠運營效率。
工廠運營現代化:智能生產管理系統的優勢
在現代化工廠運營中,智慧生產管理系統的優勢無可比擬。即時資料與視覺化是其一大亮點。這些系統提供即時更新的資料,讓管理者能隨時掌握機器效能和庫存狀態。你可以想像一下,一張圖表就能告訴你所有需要知道的資訊,這樣分析起來是不是方便多了呢?
是預測性維護。透過機器學習演演算法,智慧系統會自動分析裝置資料並提前警示何時需要維修或更換零件。不僅避免突如其來的停機,也有效提升了生產效率。
協作與溝通功能則讓不同部門的人員可以同步協作。例如,你的工程師和操作員都能在同一平台上即時分享最新進度和任務更新,大幅提高問題解決速度。這不僅省下大量時間,也使整個團隊更加緊密合作。
是預測性維護。透過機器學習演演算法,智慧系統會自動分析裝置資料並提前警示何時需要維修或更換零件。不僅避免突如其來的停機,也有效提升了生產效率。
協作與溝通功能則讓不同部門的人員可以同步協作。例如,你的工程師和操作員都能在同一平台上即時分享最新進度和任務更新,大幅提高問題解決速度。這不僅省下大量時間,也使整個團隊更加緊密合作。
Comparison Table:
系統名稱 | 主要功能 | 特色 | 最新趨勢 | 權威觀點 |
---|---|---|---|---|
台塑網MES系統 | 提高生產力、降低成本、整合生產資源及權限管理 | 具備高度自動化和靈活性,能夠快速適應變化的市場需求 | 結合邊緣運算技術,實現即時數據處理和分析,更有效支持製造過程中的決策制定。 | 業界專家認為,此系統在推動智慧製造轉型上具有重要影響力,是企業升級的關鍵工具。 |
ciMes標籤管理系統 | 範本快速設計、防錯和彈性資料來源管理 | 強大的防錯機制及可視化操作介面,大幅減少人為失誤風險,提高產品質量與生產效率。 | 採用雲端技術以增強資料存取速度,並支持多語言環境以迎合全球市場挑戰。 | 被樹立為中小企業在提升生產靈活性及應對市場變遷上的最佳實踐範本。 |
DigiFacture模組化生產管理系統 | 一站式管理全工廠機台數據,提高效率與自動化水平 | 模組化設計允許根據特定需求進行擴展,使得資源配置更加靈活且高效。 | 借助人工智慧進行預測性維護,有效降低非計劃停機時間,提升設備使用率至新高峰。 | 其創新能力受到廣泛讚譽,被視為未來智能製造的重要支柱,尤其是在歐美市場獲得高度評價。 |
MES系統(一般) | 促進自動化、資料分析和決策制定 | 作為工廠設備控制與企業營運ERP之間的重要連結,有助於全面監控生產狀態。 | 推廣物聯網 (IoT) 和雲端運算,以便加速信息流通並提高風險預警能力,是當前發展熱潮之一。 | 國際標準如ISA-95被業界普遍接受,以指導企業優化作業流程及透明度提升策略。 |
某知名品牌 MES 系統 | 智能調度、生產追蹤、自動報表生成 | 專注於能源消耗優化和人員排程最佳化,顯著提高資源利用率並減少浪費情況發生. | 利用深度學習技術進行異常檢測與品質預測,加強品質管控的主動性與精確度. | 持續參加國際展會以展示最新技術創新,被認為是引領智能製造行業未來方向的佼佼者. |
導入生產管理系統時應避免的常見陷阱
在匯入生產管理系統時,很多工廠容易掉進幾個常見陷阱。**避免紙本依賴的過渡性陷阱📄**。如果還在用紙本紀錄,那就大錯特錯了!這不但會阻礙資料整合,還容易出錯和浪費時間。不如直接上手數位化工具,例如自動化資料擷取或移動應用程式,這樣可以確保即時存取和決策。
其次是**過度客製化導致靈活度受限🔧**。雖然客製化能滿足特定需求,但太過了反而限制系統的擴充性。不妨考慮模組化解決方案或跟專家合作,平衡一下客製和標準功能,以便未來有變化也能輕鬆應對。
最後一點,就是**缺乏員工培訓和參與👥**。一套新系統要成功,全體員工的參與很重要。如果大家沒準備好就強行推行,只會事倍功半。因此,一定要提供充分培訓、聽取意見並建立持續改進文化。這樣才能讓員工更快接受新系統,也發揮它的全部潛力!
其次是**過度客製化導致靈活度受限🔧**。雖然客製化能滿足特定需求,但太過了反而限制系統的擴充性。不妨考慮模組化解決方案或跟專家合作,平衡一下客製和標準功能,以便未來有變化也能輕鬆應對。
最後一點,就是**缺乏員工培訓和參與👥**。一套新系統要成功,全體員工的參與很重要。如果大家沒準備好就強行推行,只會事倍功半。因此,一定要提供充分培訓、聽取意見並建立持續改進文化。這樣才能讓員工更快接受新系統,也發揮它的全部潛力!
量身打造最適生產管理系統:評估工廠特定需求
選擇最佳的生產管理系統並非一蹴而就,首先要徹底評估工廠的特定需求。第一步便是分析工廠格局與流程。你需要明白整個工廠的佈局,包括生產線、物料流向和裝置放置。透過這樣的全面了解,你才能找出瓶頸及低效率區域,比如哪裡浪費最多時間或資源。一些精益六西格瑪工具如價值流對映和流程圖,可以幫助你識別改善機會。
接下來,是資料收集與分析。收集有關生產、庫存、質量和成本等資料,然後利用商業智慧工具或統計流程控制來分析,這樣可以發現模式或趨勢,同時預測未來績效。
不要忽視特定產業和法規考量。例如製藥業需遵守cGMP,而食品業則需符合HACCP標準。一些通用法規如ISO 9001或FDA 21 CFR Part 11也必須納入考量範圍,以確保你的系統符合所有適用要求。
接下來,是資料收集與分析。收集有關生產、庫存、質量和成本等資料,然後利用商業智慧工具或統計流程控制來分析,這樣可以發現模式或趨勢,同時預測未來績效。
不要忽視特定產業和法規考量。例如製藥業需遵守cGMP,而食品業則需符合HACCP標準。一些通用法規如ISO 9001或FDA 21 CFR Part 11也必須納入考量範圍,以確保你的系統符合所有適用要求。
結論:邁向工廠生產管理優化之路
結論:邁向工廠生產管理最佳化之路
在選擇最佳的工廠生產管理系統時,AI 和機器學習是提升效率的重要利器。透過這些技術,我們可以精準預測維護時間、提升產品品質並有效分配資源。你是否曾想過能夠提早發現裝置問題,而不是等到故障才修理?AI 就能做到!
雲端運算讓我們不再受限於硬體裝置。不僅可以靈活擴充套件系統規模,更能簡化資料管理和強化團隊協作。試想一下,你可以隨時隨地檢視生產資料,大大提高了工作效率。
人機協作的興起改變了傳統製造業。引入協作機器人來完成重複性任務,不僅提高了生產率和產品質量,也減輕了員工負擔,讓他們專注於更具創造性的工作。同時還縮小了技能差距,使得新手也能快速上手操作。
透過整合 AI、雲端運算和人機協作,你將走在工廠生產管理最佳化的前沿。)
在選擇最佳的工廠生產管理系統時,AI 和機器學習是提升效率的重要利器。透過這些技術,我們可以精準預測維護時間、提升產品品質並有效分配資源。你是否曾想過能夠提早發現裝置問題,而不是等到故障才修理?AI 就能做到!
雲端運算讓我們不再受限於硬體裝置。不僅可以靈活擴充套件系統規模,更能簡化資料管理和強化團隊協作。試想一下,你可以隨時隨地檢視生產資料,大大提高了工作效率。
人機協作的興起改變了傳統製造業。引入協作機器人來完成重複性任務,不僅提高了生產率和產品質量,也減輕了員工負擔,讓他們專注於更具創造性的工作。同時還縮小了技能差距,使得新手也能快速上手操作。
透過整合 AI、雲端運算和人機協作,你將走在工廠生產管理最佳化的前沿。)
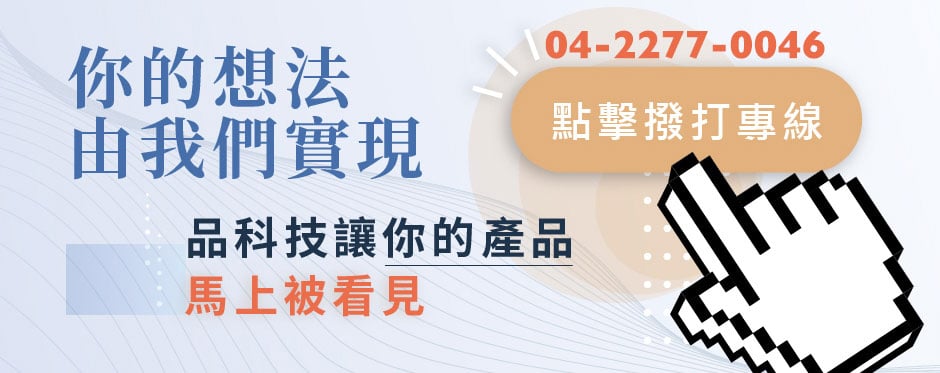