核心行動建議 - 提升可撓性OLED設計及量產成功率,降低風險與成本
- 建立嚴格材料檢驗標準,確保基材純度與塗佈均勻性誤差≤5%
避免原料瑕疵導致良率下降,提高後續製程穩定性與產品品質
- 設定封裝膜耐熱與水蒸氣阻隔性能門檻,要求達到行業主流水準以上
保護OLED元件不受環境影響延長使用壽命,減少維修及退貨成本
- 進行小規模試產時,每批次測試彎折循環至少達3000次以驗證柔韌度
確保產品符合彎曲需求,減少量產後因機械疲勞造成的失效風險
- 推動跨部門協作會議每週召開一次,同步解決封裝延遲和良率異常問題
加速問題回饋與決策過程,提高整體生產效率和產品一致性
小規模試產,先試後量產的冒險與緩衝
我們團隊那時候,欸,第一次要搞可撓式有機發光二極體顯示面板的時候,老實說最一開始真的是被結構設計跟材料彎折這兩個鬼東西搞得有點頭大。像是摺疊手機的原型嘛,我們就一直在調薄膜封裝啊、主動矩陣排列那些細節,弄到後來我自己都快分不清到底是哪個環節出錯——唉,總之就是換了又換,各種層間壓合工藝都試過才慢慢摸索到一組能讓畫質穩定下來、同時又比較不會隨便生出什麼討人厭折痕的做法。
然後其實,有些同事還突然跑去聊汽車螢幕怎樣怎樣(好啦,我也八卦了一下),但拉回來講重點啦,就是我們特別把端點應用需求這塊擺很前面。比如車載顯示設備常常要配合一些奇形怪狀的曲面安裝,你沒提早預估現場操作情境真的很容易全軍覆沒。所以我覺得,多做幾輪模擬測試咧、多場景連著驗證彎折壽命,加上你如果願意優先選用那些已經通過大規模可靠性評比的基材,其實可以省掉不少冤枉路,也減少初期一堆失敗帶來的不爽。
其實仔細想想,每次糾結這些瑣碎細節,好像都是決定柔性螢幕技術最後到底能不能真正落地應用、或是只能躲在理論裡自嗨吧。有時候忙著測試,很想直接放空,但還是忍不住會想,到底哪一步才算穩妥?
然後其實,有些同事還突然跑去聊汽車螢幕怎樣怎樣(好啦,我也八卦了一下),但拉回來講重點啦,就是我們特別把端點應用需求這塊擺很前面。比如車載顯示設備常常要配合一些奇形怪狀的曲面安裝,你沒提早預估現場操作情境真的很容易全軍覆沒。所以我覺得,多做幾輪模擬測試咧、多場景連著驗證彎折壽命,加上你如果願意優先選用那些已經通過大規模可靠性評比的基材,其實可以省掉不少冤枉路,也減少初期一堆失敗帶來的不爽。
其實仔細想想,每次糾結這些瑣碎細節,好像都是決定柔性螢幕技術最後到底能不能真正落地應用、或是只能躲在理論裡自嗨吧。有時候忙著測試,很想直接放空,但還是忍不住會想,到底哪一步才算穩妥?
需求驅動下,從特殊應用到全面普及的柔性浪潮
根據產業調查,還有唉,有些供應鏈的案例吧,每次企業第一次想把可撓式OLED弄到產品設計裡,預算總是抓不太準。嗯,我說真的,那種一開始專案時大家都很容易被展示會上那些漂亮參數吸過去,好比什麼表面彎折半徑只有幾毫米、壽命測試能扛個數萬次,看起來很厲害。但等到你真的要量產了,才發現事情沒那麼單純——材料批次之間的差異像是突然冒出來的小怪獸,然後封裝工藝的穩定性又搞得人頭痛。
欸我剛剛是不是有點離題?對啦,反正就是不同終端設備還會各自要求品質控管標準,有時候光這一項就能讓專案進度變慢,本來以為能趕得上的時程一下子拖延了,而且成本甚至可能翻倍超過原本估算。其實從研發部門到採購端,中間細節一大堆,小地方磨合不起眼,但連帶影響整個局勢也不是沒可能。嗯,有經驗的人或許懂,可缺乏經驗嘛……那學費喔,很快就付掉兩三輪了。好吧,就是這樣。
欸我剛剛是不是有點離題?對啦,反正就是不同終端設備還會各自要求品質控管標準,有時候光這一項就能讓專案進度變慢,本來以為能趕得上的時程一下子拖延了,而且成本甚至可能翻倍超過原本估算。其實從研發部門到採購端,中間細節一大堆,小地方磨合不起眼,但連帶影響整個局勢也不是沒可能。嗯,有經驗的人或許懂,可缺乏經驗嘛……那學費喔,很快就付掉兩三輪了。好吧,就是這樣。
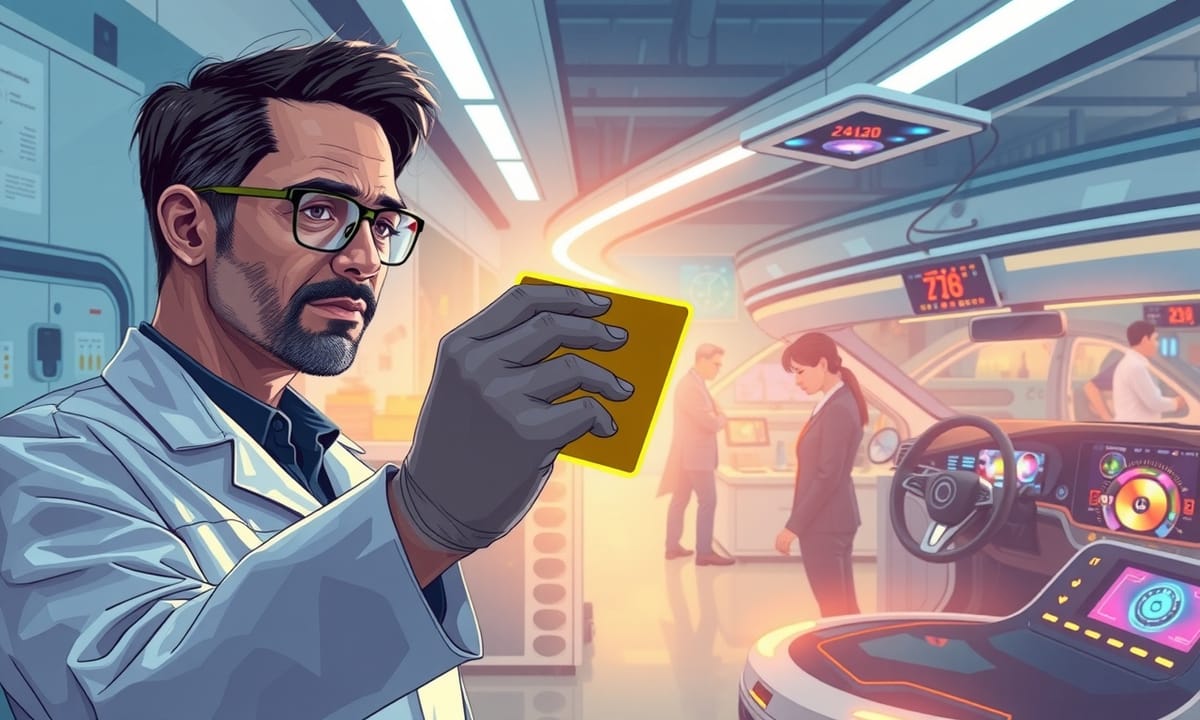
跨部門溝通卡關?封裝延遲與良率焦慮並存
「我們遇到最大的壓力,就是量產時材料規格批次不一致,導致成品良率掉到預期以下。」有個工程主管這樣講的時候,我腦袋裡忍不住開始飄走,好像突然想到上週沒繳電費。唉,但說回來,可撓式OLED這技術雖然近年確實有點突破啦,真正到了設計階段卻很容易卡住。成本常常控不下來、然後可靠度驗證也總是複製失敗,有些步驟試了又試還是不行。大規模生產?風險就像天氣一樣難以預料。
其實亞洲供應商那邊,例如智晶光電,他們選的是比較穩健的路線。嗯——不是那種一飛沖天的戲碼,而是漸進地優化核心材料TADF/HF,還有封裝工藝,不急著一步登天。不過話說回來,他們在亮度提升方面真的做得蠻猛,據說都快要接近原本兩倍了。但細節處理起來還是麻煩,每個客戶都會挑剔不同細部參數,只能反覆調整,一遍又一遍。有時我會想,要不要乾脆全部標準化算了?可是現實總是讓人打臉。
這種連續累積、逐步微調的方法嘛,跟西方企業偏愛搞單點重大突破很不一樣,也許靈活性高一些,可以對應市場突如其來的小變動吧。不過老實說,每次跨代升級,其實都在默默消耗團隊的人力和時間資源,而且感覺每輪投入完心情就又被掏空一次。有點疲憊齁,但好像也只能這樣繼續下去。
其實亞洲供應商那邊,例如智晶光電,他們選的是比較穩健的路線。嗯——不是那種一飛沖天的戲碼,而是漸進地優化核心材料TADF/HF,還有封裝工藝,不急著一步登天。不過話說回來,他們在亮度提升方面真的做得蠻猛,據說都快要接近原本兩倍了。但細節處理起來還是麻煩,每個客戶都會挑剔不同細部參數,只能反覆調整,一遍又一遍。有時我會想,要不要乾脆全部標準化算了?可是現實總是讓人打臉。
這種連續累積、逐步微調的方法嘛,跟西方企業偏愛搞單點重大突破很不一樣,也許靈活性高一些,可以對應市場突如其來的小變動吧。不過老實說,每次跨代升級,其實都在默默消耗團隊的人力和時間資源,而且感覺每輪投入完心情就又被掏空一次。有點疲憊齁,但好像也只能這樣繼續下去。
巨頭獨占下的五百億藍海與綠色工藝新競技場
「你們到底是怎麼算柔性螢幕的生產預算?」這句話是2023年在上海展會時,一位法國顧問突然冒出的問題。嗯,現場那幾個做材料的老闆聽到後,就像一時間都沒反應過來,有點尷尬地互看。好吧,其實全球市場是不是特別火熱呢?說真的,眼下歐美還有韓國那邊,出貨量基本還壓著一半左右——感覺他們靠的是那些技術專利庫。啊,我差點忘了,亞洲新興品牌也不是吃素的,他們最近好像開始從低階慢慢想往高端鑽,也許哪天市占率就悄悄浮起來,你懂得。
結果講到2025年產值怎麼估……這裡就亂成一團,各家顧問公司口徑根本合不攏。有些超樂觀,直接喊去年的三成增長;但也有人明顯收斂,只肯說什麼「溫和微升」,讓人聽了很無力。欸,不對,我又岔題了。拉回來講台灣電子業圈子好了——私底下常流傳一句話:如果產品設計預期抓錯,柔性螢幕光是改版開模費就能把成本推高數十倍。有夠誇張。不管全球總額再亮眼,只要需求方向偏掉、技術彈性判斷失準,很可能所有漂亮數字一下子全被額外花費吞噬乾淨,好啦,就是這麼現實。
結果講到2025年產值怎麼估……這裡就亂成一團,各家顧問公司口徑根本合不攏。有些超樂觀,直接喊去年的三成增長;但也有人明顯收斂,只肯說什麼「溫和微升」,讓人聽了很無力。欸,不對,我又岔題了。拉回來講台灣電子業圈子好了——私底下常流傳一句話:如果產品設計預期抓錯,柔性螢幕光是改版開模費就能把成本推高數十倍。有夠誇張。不管全球總額再亮眼,只要需求方向偏掉、技術彈性判斷失準,很可能所有漂亮數字一下子全被額外花費吞噬乾淨,好啦,就是這麼現實。
引用來源:
- Oled Displays Market Size, Share and Forecast, 2025-2032
Pub.: 2025-02-19 | Upd.: 2025-06-05 - Flexible OLEDs: introduction and market status
Pub.: 2025-06-15 | Upd.: 2025-05-12 - Flexible OLED Display Market Size, Share & Report, 2033
Pub.: 2025-06-24 | Upd.: 2025-07-05 - Flexible OLED Display Market Size, Share, Trend and Forcarst to 2025
- Flexible OLED Market Size & Share Analysis - Mordor Intelligence
Pub.: 2025-04-28 | Upd.: 2025-07-11
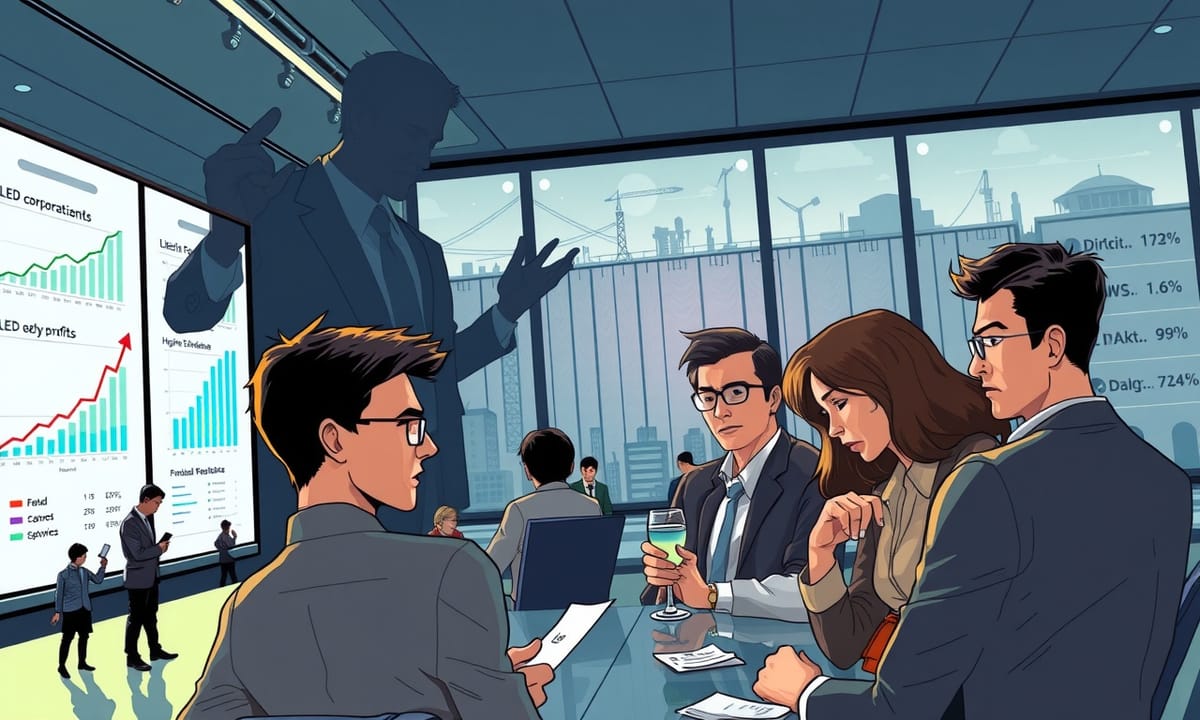
原料、沉積、環控——烘焙細節與品質底線
「只要量產規模一拉大,細節就全被放大檢視。」嗯,這是產線資深工程師常掛在嘴邊的話,其實我第一次聽到還以為只是老鳥碎念,但後來才發現…真的沒在開玩笑。你想把可撓性OLED從實驗室推進到量產?每個步驟都像拆炸彈一樣要精確,不然下一秒爆掉的就是自己。先說環境潔淨度好了,標準低一點都不行,有時候光是一顆微粒鑽進多層結構,唉,你根本連測試階段都碰不到——講到這裡忽然想到,那些防塵服穿了好幾層還會偷懶脫掉嗎?呃,好啦,我又岔題了。
拉回來講,多層材料堆疊那個對位真的是關鍵,要是有半點偏差,接下來良率掉得比你想像還快,有時候一夜回頭看數據整個人都傻住。roll-to-roll製程也是讓人抓狂的一環,張力和速度必須死盯著調,不然基板不是拉長變形,就是直接斷給你看,那種挫敗感很難形容。
至於封裝階段,防潮膜厚度與覆蓋均勻度得逐批檢查,每次驗收都覺得像考試。有經驗的團隊甚至會再設一組獨立驗證站點——其實也不能怪他們小心眼,只是吃過太多虧罷了。哪個步驟省略、隨便帶過,都超容易出不可逆風險,而且最近幾年亞洲新興廠商已經反覆踩雷,新聞報導有時候都寫膩了吧。不知道是不是大家都有類似的無奈感……但總之,每一道工序都是修羅場。
拉回來講,多層材料堆疊那個對位真的是關鍵,要是有半點偏差,接下來良率掉得比你想像還快,有時候一夜回頭看數據整個人都傻住。roll-to-roll製程也是讓人抓狂的一環,張力和速度必須死盯著調,不然基板不是拉長變形,就是直接斷給你看,那種挫敗感很難形容。
至於封裝階段,防潮膜厚度與覆蓋均勻度得逐批檢查,每次驗收都覺得像考試。有經驗的團隊甚至會再設一組獨立驗證站點——其實也不能怪他們小心眼,只是吃過太多虧罷了。哪個步驟省略、隨便帶過,都超容易出不可逆風險,而且最近幾年亞洲新興廠商已經反覆踩雷,新聞報導有時候都寫膩了吧。不知道是不是大家都有類似的無奈感……但總之,每一道工序都是修羅場。
百台長測揭密:封裝驗證到底怎麼做才夠嚴謹
新創企業想踏進可撓性OLED量產這條路,最麻煩的通常還不是什麼技術本身啦(唉,其實技術當然也很難),反而是誰有膽子扛風險、誰能精準調配那些本來就不夠用的資源。嗯,最近工研院不是都有在講嗎?他們觀察到不少剛起步的團隊,在規劃設計時會過分自信自己的研發能力,然後有些人又乾脆把供應鏈重構那層算得太輕,結果一碰到驗證階段就卡住——進退兩難喔,那種窒息感你懂吧。
說回來,有經驗的人都會先整理清楚:自己到底哪些技術才是本錢?比方說聚醯亞胺塗佈、薄膜轉印或超薄封裝這些基礎工藝,到底自己行不行;再檢查一下跨部門人力,看是不是能支援機電整合或系統模組化開發。欸,我剛想到我午餐是不是忘記吃水果了……呃,拉回來。此外啊,他們還要盤點現有合作夥伴對材料供應和設備維護的反應速度,就是直接問清楚:哪些製程外包沒問題,哪些環節非得自己做不可。
曾經有人圖方便,把全部都委外了,可惜規格溝通搞砸,良率最後只剩下原先估算的大約三成,氣死人。有另外一些堅持親力親為,但人才斷層就活生生讓流程停滯不前,也是悶壞。總之吧,好像還是根據自身強項去設計那種分階段切入、又預留彈性調整空間的方法比較保險——畢竟資源有限時,要犯重大錯誤其實並不難,所以…嗯,大概就是這樣了。
說回來,有經驗的人都會先整理清楚:自己到底哪些技術才是本錢?比方說聚醯亞胺塗佈、薄膜轉印或超薄封裝這些基礎工藝,到底自己行不行;再檢查一下跨部門人力,看是不是能支援機電整合或系統模組化開發。欸,我剛想到我午餐是不是忘記吃水果了……呃,拉回來。此外啊,他們還要盤點現有合作夥伴對材料供應和設備維護的反應速度,就是直接問清楚:哪些製程外包沒問題,哪些環節非得自己做不可。
曾經有人圖方便,把全部都委外了,可惜規格溝通搞砸,良率最後只剩下原先估算的大約三成,氣死人。有另外一些堅持親力親為,但人才斷層就活生生讓流程停滯不前,也是悶壞。總之吧,好像還是根據自身強項去設計那種分階段切入、又預留彈性調整空間的方法比較保險——畢竟資源有限時,要犯重大錯誤其實並不難,所以…嗯,大概就是這樣了。
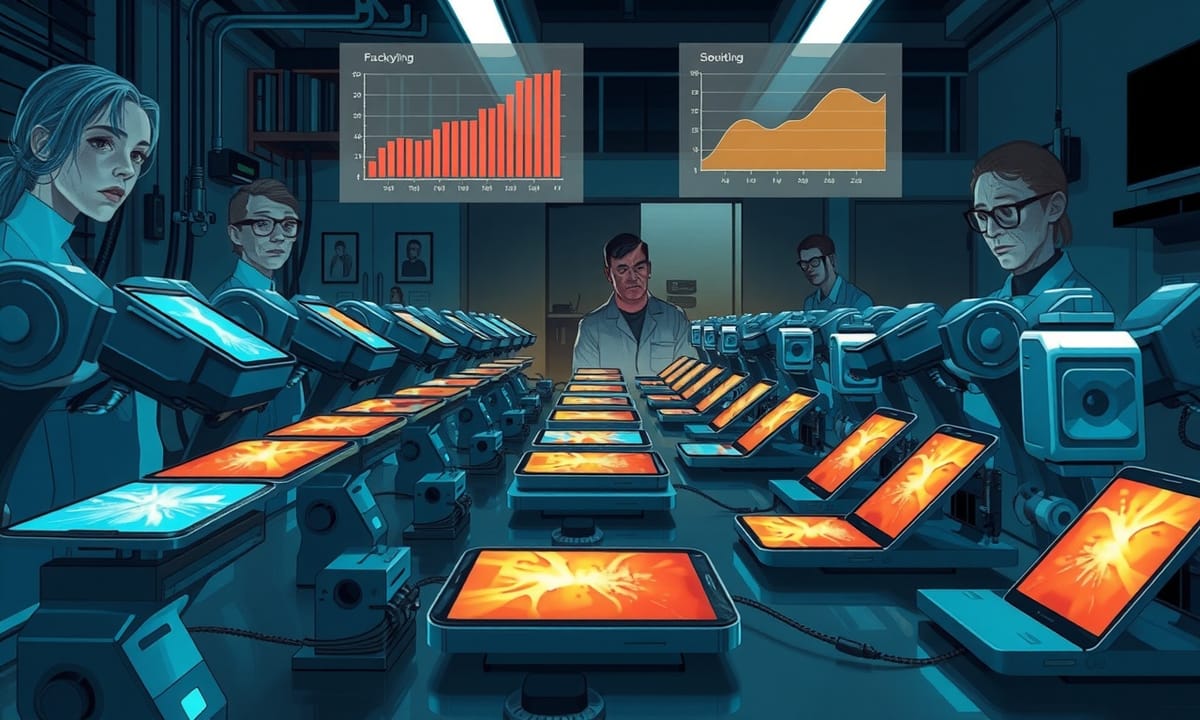
供應鏈彈性規劃,備援網絡防單點失效危機
德國萊因這類第三方實驗室,嗯,近年不是一直在講可撓性OLED檢測流程嗎?他們通常會先定個樣本量,大概一百台左右,看起來有點隨便但其實是為了統計基礎夠紮實。我以前以為五十台就行欸,但好像不夠啦。然後,他們還得細細規劃整個測試期間,有時要安排加速老化——那種模擬一年以上使用環境的(說真的,誰家一年內彎壞兩次啊),而且條件層層疊疊,包括溫度、濕度跟機械彎折什麼都算進去。唉,我每次看到那些變數表就頭痛。
說到失效率指標,其實不能偷懶只記單點失效,一定得畫出失效分布圖才比較踏實,不然你怎麼知道各種封裝技術在不同狀況下會差多遠?對啦,中間我有時候忍不住想,如果工程師們都照書做事,是不是還會漏掉長期風險呢……喔對,要是只拿一次報告來看、或根本沒把失效模式分門別類,那真的很危險,感覺一大堆坑沒補。反正建立那種跨時段、多面向資料庫好像蠻重要的吧,可以讓品質工程師去判斷到底哪些技術值得繼續丟資源下去。不過話又說回來,每天盯著這些資料也挺累人的。
說到失效率指標,其實不能偷懶只記單點失效,一定得畫出失效分布圖才比較踏實,不然你怎麼知道各種封裝技術在不同狀況下會差多遠?對啦,中間我有時候忍不住想,如果工程師們都照書做事,是不是還會漏掉長期風險呢……喔對,要是只拿一次報告來看、或根本沒把失效模式分門別類,那真的很危險,感覺一大堆坑沒補。反正建立那種跨時段、多面向資料庫好像蠻重要的吧,可以讓品質工程師去判斷到底哪些技術值得繼續丟資源下去。不過話又說回來,每天盯著這些資料也挺累人的。
保守派vs.創新黨:設計選型該循序還是激進?
某次業界討論會上,嗯,有人突然丟了一句:可撓性OLED要是聚醯亞胺基板原料那邊一出狀況,整條生產線就像被卡住動彈不得,欸,其實被影響的不只交貨期這麼單純。資深供應鏈顧問有時會不經意補充一句,他說這種新型顯示器麻煩得很,每個細節攤開來都能寫成專案報告,重建上下游網絡根本耗神。講著講著我忽然想起那天午餐吃什麼——咦,不重要啦,拉回來。
表面上換材料廠商看似備案簡單,但現場工程師都清楚,只要涉及特殊塗佈或設備對接的東西,流程驗證幾乎等於要從頭開始跑一遍,好累啊。有些製造端主管曾分享過,看起來亞洲幾個主要國家合計拿下將近一半市占,好像很厲害,可事實上地理高度集中讓風險變大了不少——去年日本某設備維修延誤,就是直接導致有品牌產品上市推遲。
你說經理嗎?有人總習慣只簽一家供應來源,其實也不知道哪裡來的自信;老手反倒會早早找好備援路徑,有時還跟技術團隊一起盤點,到底能不能用次級替代品先撐急單。聽他們說,把錢花在備案預算上,比臨時停工省太多啦。唉,人就是這樣吧,一到出事才在後悔當初沒準備。
表面上換材料廠商看似備案簡單,但現場工程師都清楚,只要涉及特殊塗佈或設備對接的東西,流程驗證幾乎等於要從頭開始跑一遍,好累啊。有些製造端主管曾分享過,看起來亞洲幾個主要國家合計拿下將近一半市占,好像很厲害,可事實上地理高度集中讓風險變大了不少——去年日本某設備維修延誤,就是直接導致有品牌產品上市推遲。
你說經理嗎?有人總習慣只簽一家供應來源,其實也不知道哪裡來的自信;老手反倒會早早找好備援路徑,有時還跟技術團隊一起盤點,到底能不能用次級替代品先撐急單。聽他們說,把錢花在備案預算上,比臨時停工省太多啦。唉,人就是這樣吧,一到出事才在後悔當初沒準備。
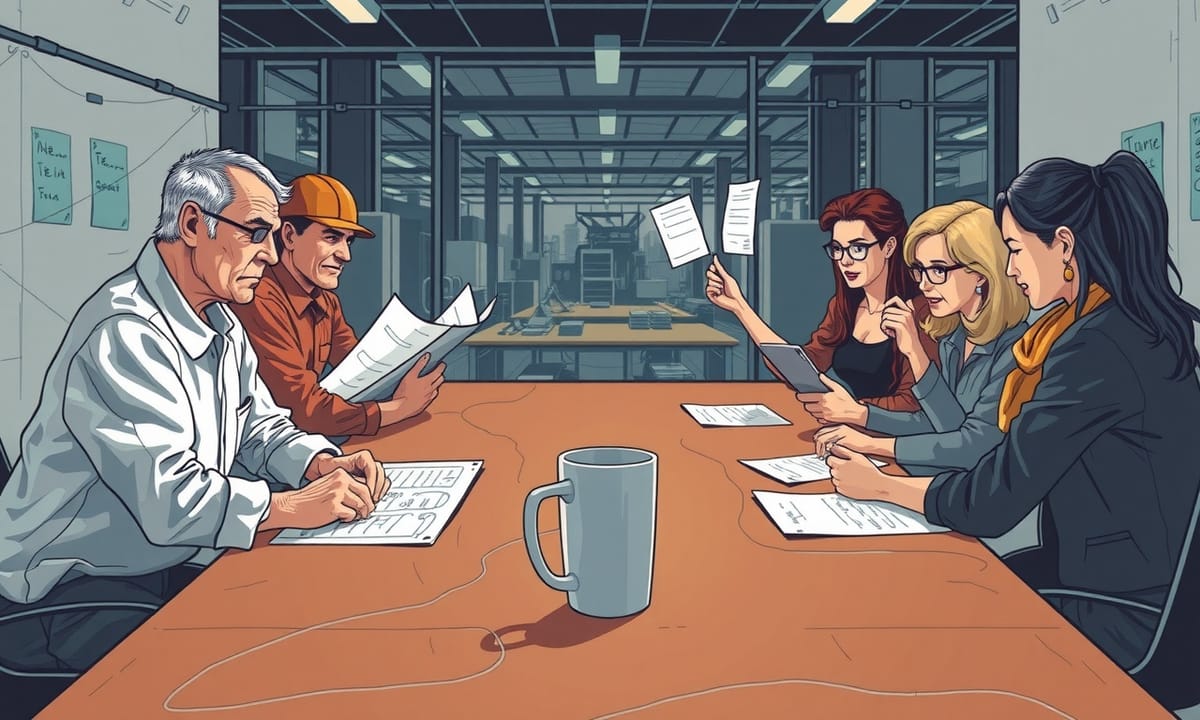
高維護費用是假象?其實真正燒錢在前端研發
「柔性螢幕就是高風險、一定貴出許多」這種說法,唉,業界裡頭聽久了也會覺得膩,但現實根本沒這麼簡單啦。還記得2023年去韓國參加顯示器展,現場跟幾個工程師隨口聊,他們一邊哈欠一邊說,現在不少廠早就靠材料改質和製程優化,把可撓性OLED的良率慢慢追上傳統平面了。有些更狠,直接搞模組標準化、工序共享,硬是把那些超貴的設備成本平均到不同產品線——講白話一點,就是昂貴沒錯,但不是只能燒錢,分給多個應用吃下去,單價自然就壓下來了。
像智晶光電就是個很妙的例子,他們沒走人家都在搶的那條路,反而轉進醫療健康領域,拿柔性OLED來做皮膚治療、光療設備這種比較冷門但很實用的應用。與其說技術炫不炫,不如說他們的思路更接地氣——讓技術不是拿來堆規格,而是真的解決某些現場的需求,這種差異化,其實才是關鍵。
說回來,如果真的執著於極端客製化或非得要什麼最高彎曲性能,那驗證週期拖得老長也是正常;供應鏈嘛,也會變得更敏感,一風吹草動就搞不定。欸對,有時候我會突然懷疑:技術方案真有那麼可怕嗎?其實正確評估到底是不是高風險、高成本,你不能只看產品類型啦,要把設計路線、市場策略、備援配置全都拉進來思考才行。不然咧,就只是無止盡地嚼舊話題,人生多無趣啊。
像智晶光電就是個很妙的例子,他們沒走人家都在搶的那條路,反而轉進醫療健康領域,拿柔性OLED來做皮膚治療、光療設備這種比較冷門但很實用的應用。與其說技術炫不炫,不如說他們的思路更接地氣——讓技術不是拿來堆規格,而是真的解決某些現場的需求,這種差異化,其實才是關鍵。
說回來,如果真的執著於極端客製化或非得要什麼最高彎曲性能,那驗證週期拖得老長也是正常;供應鏈嘛,也會變得更敏感,一風吹草動就搞不定。欸對,有時候我會突然懷疑:技術方案真有那麼可怕嗎?其實正確評估到底是不是高風險、高成本,你不能只看產品類型啦,要把設計路線、市場策略、備援配置全都拉進來思考才行。不然咧,就只是無止盡地嚼舊話題,人生多無趣啊。
敏捷文化落地,橫向共創打造不敗組織結構
嗯,全面方案整合這件事嘛,其實現場上大家常說要從材料選型、製程流程設計到應用端測試一起規劃,結果大部分時候還是有人只顧一頭吧。唉,但現實蠻殘酷的——據經驗,那些有跨領域協作能力,又能做垂直整合的團隊,才真的比較快把東西導入量產線,而且也比較不會遇到什麼材料斷鏈或技術磨合搞得人仰馬翻。這個說法好像聽起來很老生常談?欸,不過數據就是這樣。
然後操作細節,有時候真的是只能一步步來,你可以分階段驗證,像先挑幾十件樣品去跑溫濕度循環、彎折壽命之類加速測試,反正沒測完總覺得心裡毛毛的。啊對,我剛剛想到中午吃什麼...咳咳拉回來。等前面撐過去了,再看 roll-to-roll 製程跟噴墨印刷這種量產工藝到底合不合拍,適配性問題早解決晚解決差很多。
至於工具方面啦,可以試著把柔性封裝模組標準和全流程環境監控系統串起來,其實這種做法常讓你在初期就發現那些討人厭的製程變異點。我有次太晚裝監控結果爆單,好煩喔!如果你手上的供應鏈資源又不是那麼充裕,大概還是要優先弄一份聚醯亞胺基板、還有關鍵有機材料的備援清單放著,比較不會生產卡住,到最後客戶催都沒辦法交貨。
另外產品定義那塊,也最好一開始就思考「適配性創新」原則啦,就是針對特定市場需求動態調校設計參數,不需要死命追求什麼極致性能指標……其實穩穩地達成量產才是真的容易活下去。有時候想太多也只是自己累而已,好吧。
然後操作細節,有時候真的是只能一步步來,你可以分階段驗證,像先挑幾十件樣品去跑溫濕度循環、彎折壽命之類加速測試,反正沒測完總覺得心裡毛毛的。啊對,我剛剛想到中午吃什麼...咳咳拉回來。等前面撐過去了,再看 roll-to-roll 製程跟噴墨印刷這種量產工藝到底合不合拍,適配性問題早解決晚解決差很多。
至於工具方面啦,可以試著把柔性封裝模組標準和全流程環境監控系統串起來,其實這種做法常讓你在初期就發現那些討人厭的製程變異點。我有次太晚裝監控結果爆單,好煩喔!如果你手上的供應鏈資源又不是那麼充裕,大概還是要優先弄一份聚醯亞胺基板、還有關鍵有機材料的備援清單放著,比較不會生產卡住,到最後客戶催都沒辦法交貨。
另外產品定義那塊,也最好一開始就思考「適配性創新」原則啦,就是針對特定市場需求動態調校設計參數,不需要死命追求什麼極致性能指標……其實穩穩地達成量產才是真的容易活下去。有時候想太多也只是自己累而已,好吧。
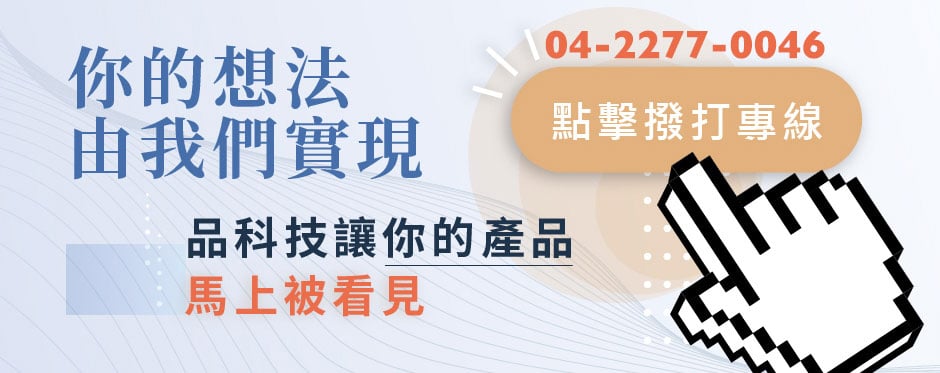