核心行動建議 - 讓APS排程系統發揮最大效益,急單插單不再失控
- 定期檢查主檔資料完整性,每月針對關鍵物料與工序進行覆核。
數據錯誤會直接導致排程混亂,提升交期準確率可達10%以上。
- 預留至少10%產能彈性專門處理急單或臨時插單。
減少換線、停機次數,現場調度壓力明顯降低,應變更快。
- 每週盤點一次設備保養紀錄並及早安排維護時段。
防止突發停機拖慢全廠節奏,有效提升訂單準時交付率。
- 設定KPI外的異常回報管道,例如遇到超過8小時未解決的瓶頸即通報管理層。
*隱性風險*可及早處理,不再等到熬夜救火才發現問題。
APS導入革命?數據真假與人機角力
工廠裡的現場主管啊,時常會提起,導入什麼高級生產計畫排程(APS)、還有那些智能製造協同系統之後,欸,其實操作確實是變精細了沒錯,整個作業調度也好像更即時,但人員反而對那堆從系統吐出來的數據準確性變得超級在意。嗯,有些老經驗的師傅,他們不太會完全照單全收自動生成的排程,總是在現場遇到突發狀況,比如說機台突然壞掉或物料晚到——這種時候就忍不住手癢自己再微調一下。話說我前幾天還聽誰抱怨過這個……唉,算了拉回來講。
專家倒是覺得這種人機合作,很像給工廠裝了導航工具啦,可真正該怎麼走、要不要繞路,其實還是靠現場那群人的經驗去彈性調整。其實也不能說太依賴哪一邊,大概就是互補吧。有時想想,數據當然重要,可你看每次出包都還是要靠人救火。嗯,所以啦,「怎麼把真實數據即時回饋給系統,還能在例外狀況下及時反應」,一直被認為是導入這些系統過程裡最棘手又不能忽視的核心挑戰。坦白講,有些問題可能連開發商自己都搞不太清楚吧?
專家倒是覺得這種人機合作,很像給工廠裝了導航工具啦,可真正該怎麼走、要不要繞路,其實還是靠現場那群人的經驗去彈性調整。其實也不能說太依賴哪一邊,大概就是互補吧。有時想想,數據當然重要,可你看每次出包都還是要靠人救火。嗯,所以啦,「怎麼把真實數據即時回饋給系統,還能在例外狀況下及時反應」,一直被認為是導入這些系統過程裡最棘手又不能忽視的核心挑戰。坦白講,有些問題可能連開發商自己都搞不太清楚吧?
主檔資料漏洞,亂流往往從小事開始
唉,據說業界那些顧問們常在講一件事──有超過七十家大型製造廠,在導APS之前最容易踩雷的地方,就是...怎麼講,總之他們老是忽略把基礎資料盤整好。這其實聽起來有點陳腔濫調,但偏偏大家就是會犯。像機台保養進度啊、BOM(物料清單)或者現有庫存,那些主檔如果還只是躺在紙本裡,或是各部門自己搞一份獨立表格——嗯,我突然想到我以前也碰過這種狀況,有夠亂——反正,這樣根本沒辦法確保資訊同步,也難怪系統最後無法即時反映現場實情。好吧。
比較理想的作法,大概應該先規劃每日或每班固定盤點流程,再由負責人當下直接把數據登錄到共用平台去。說真的,中間要是插個跨部門例會,也許就能馬上釐清突發插單、急件優先順序變動那類雜事。我自己想像那畫面,其實滿混亂的,不過有效啦。如果只靠定期彙整和事後補登?唉,那交期一定會大亂套,更別提重工損失什麼的。
再繞回主題,如果可以趁APS正式啟動前,把這些細節都先處理妥當,即便你們還沒做到全數位化,資料品質也會瞬間拉高不少。而且,人跟系統之間的協作接下來肯定順得多……話雖如此,好像又很難每次都這麼周全。但嘛,就盡量啦。
比較理想的作法,大概應該先規劃每日或每班固定盤點流程,再由負責人當下直接把數據登錄到共用平台去。說真的,中間要是插個跨部門例會,也許就能馬上釐清突發插單、急件優先順序變動那類雜事。我自己想像那畫面,其實滿混亂的,不過有效啦。如果只靠定期彙整和事後補登?唉,那交期一定會大亂套,更別提重工損失什麼的。
再繞回主題,如果可以趁APS正式啟動前,把這些細節都先處理妥當,即便你們還沒做到全數位化,資料品質也會瞬間拉高不少。而且,人跟系統之間的協作接下來肯定順得多……話雖如此,好像又很難每次都這麼周全。但嘛,就盡量啦。
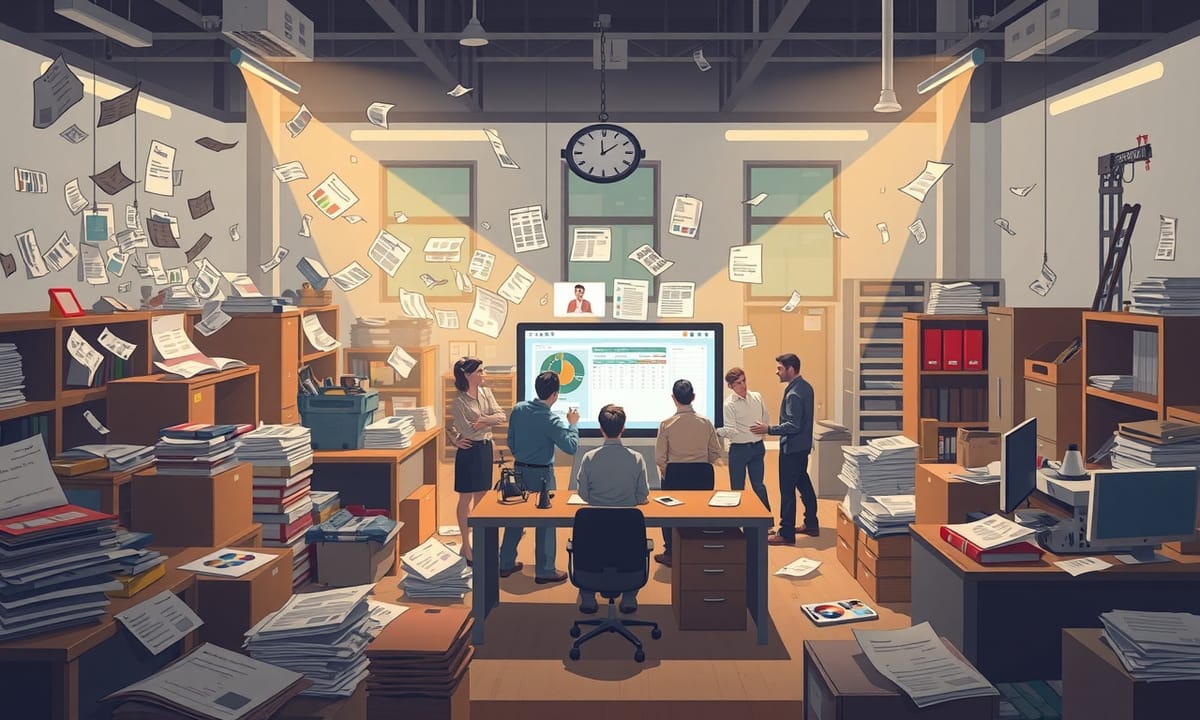
急單插隊怎解?流程細節與微調空間
唉,說真的,每次講到APS系統啟動,腦袋就有點打結。顧問們總是嘮叨著第一步要去盤查主檔資料,像設備狀態啦、BOM啦,還有那些在製品跟現有庫存,全都得一條一條核對,有時候覺得自己快變成數字機器人。嗯,可是也沒辦法,因為他們很堅持資料完整性與即時性這件事──不然後面流程根本跑不起來。
啊對了,我剛剛還想起早餐好像沒吃,不過算了,先講主題。總之把資料盤點好以後,就要設計那種每天或每班的例外事件回報流程。比方臨時插單、產線出現什麼詭異異常,又或者突然有急件需求冒出來,都必須要讓現場人員立刻在平台上登錄。我經常懷疑有人真的會天天乖乖填嗎?不過流程就是這麼規定的。
然後再下一步,他們會要求用模擬訂單來測試排程反應,比如你同時間丟很多急單進去,看系統自動調度結果跟人工微調到底差別多大。有時候看那個跑單畫面都快睡著了,但偶爾又會被某個數據嚇醒。欸,我差點忘記重點——這樣做才能比較出自動化跟人的直覺誰強。
最後嘛,為了避免資訊錯漏掉進黑洞,要特地預留手動修正介面,而且還得訂清楚跨部門溝通的路徑。搞這麼複雜,就只是希望萬一哪裡突然又冒出什麼怪狀況,可以瞬間同步到所有相關單位。不知道為什麼寫到這都覺得壓力山大,但理論上啦,這樣的流程設計確實能讓現場人在急難事件發生時,更靈活、更精準地處理吧。嗯,大概如此。
啊對了,我剛剛還想起早餐好像沒吃,不過算了,先講主題。總之把資料盤點好以後,就要設計那種每天或每班的例外事件回報流程。比方臨時插單、產線出現什麼詭異異常,又或者突然有急件需求冒出來,都必須要讓現場人員立刻在平台上登錄。我經常懷疑有人真的會天天乖乖填嗎?不過流程就是這麼規定的。
然後再下一步,他們會要求用模擬訂單來測試排程反應,比如你同時間丟很多急單進去,看系統自動調度結果跟人工微調到底差別多大。有時候看那個跑單畫面都快睡著了,但偶爾又會被某個數據嚇醒。欸,我差點忘記重點——這樣做才能比較出自動化跟人的直覺誰強。
最後嘛,為了避免資訊錯漏掉進黑洞,要特地預留手動修正介面,而且還得訂清楚跨部門溝通的路徑。搞這麼複雜,就只是希望萬一哪裡突然又冒出什麼怪狀況,可以瞬間同步到所有相關單位。不知道為什麼寫到這都覺得壓力山大,但理論上啦,這樣的流程設計確實能讓現場人在急難事件發生時,更靈活、更精準地處理吧。嗯,大概如此。
全自動神話碎片:KPI以外的日常風險
某廠區的顧問有次提到,APS剛上線那陣子,現場主管總覺得只要按下排程鍵,就像按了什麼開關——一秒瓶頸全消失。唉,這種期待感,其實還不是以前ERP廣告給灌輸的印象。說實在話,你真的繞工廠走上一圈才曉得,只要設備狀態有半點回報延誤、或是某個關鍵數據跟生產流程出現丁點脫節,那產能規劃馬上就會哪裡怪怪的。
欸,有時候腦子突然閃過午餐吃什麼…啊,拉回來講,在製品堆滿整間倉庫,可偏偏又缺料,交期還被擠壓成一團快喘不過氣。這種情形其實不少人遇過啦——據說在台灣地區近幾年導入案例中,大約七十多成新進IT夥伴都踩過坑。短暫KPI數字改善很容易讓大家放鬆警戒,好像找到救命符似的,但如果主檔沒定期更新、異常訊息沒立刻維護,一旦偷懶一下,下場通常就是後患無窮。
大部分人都覺得只要系統自動推算就行,其實更正確的做法應該是,每次例外處理都必須知識化,例如建立跨部門共用紀錄表,好讓每筆修正都有溯源依據;而不是光靠那機器自己想辦法。不然流於表面順暢之下,底層問題只會悄悄積累,到最後連誰漏掉哪個環節也搞不清楚…好吧,人腦畢竟還是比演算法碎嘴多了點。
欸,有時候腦子突然閃過午餐吃什麼…啊,拉回來講,在製品堆滿整間倉庫,可偏偏又缺料,交期還被擠壓成一團快喘不過氣。這種情形其實不少人遇過啦——據說在台灣地區近幾年導入案例中,大約七十多成新進IT夥伴都踩過坑。短暫KPI數字改善很容易讓大家放鬆警戒,好像找到救命符似的,但如果主檔沒定期更新、異常訊息沒立刻維護,一旦偷懶一下,下場通常就是後患無窮。
大部分人都覺得只要系統自動推算就行,其實更正確的做法應該是,每次例外處理都必須知識化,例如建立跨部門共用紀錄表,好讓每筆修正都有溯源依據;而不是光靠那機器自己想辦法。不然流於表面順暢之下,底層問題只會悄悄積累,到最後連誰漏掉哪個環節也搞不清楚…好吧,人腦畢竟還是比演算法碎嘴多了點。
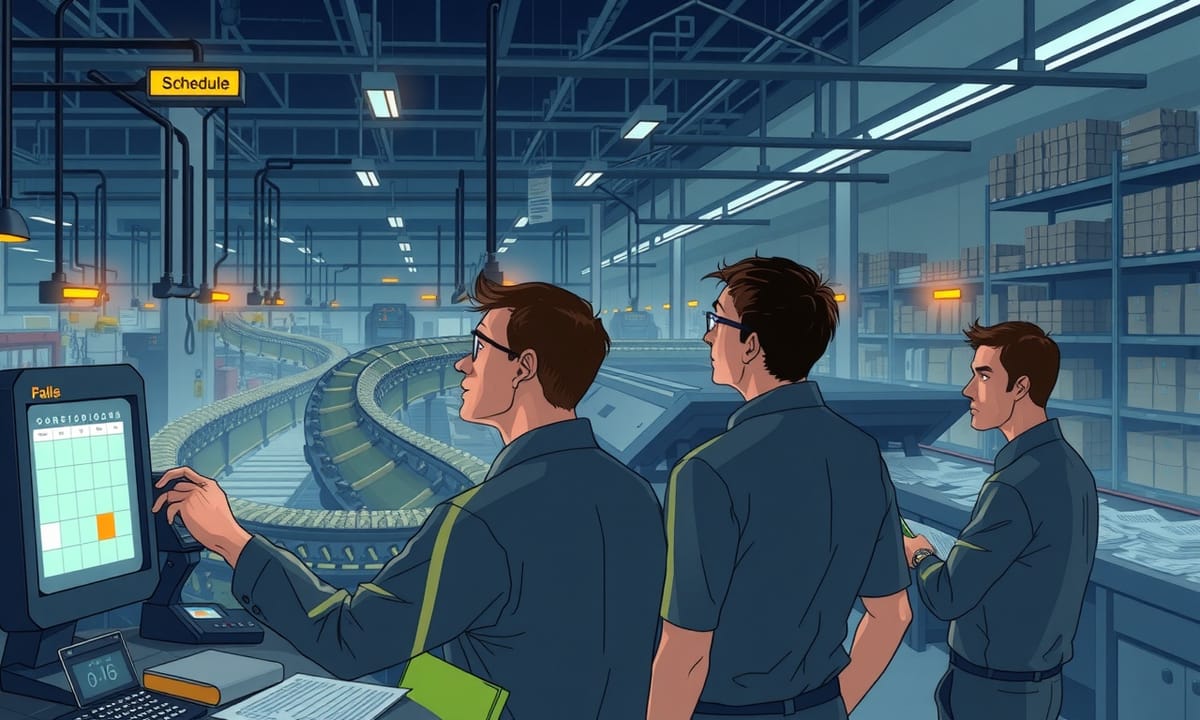
亞洲默契還是歐美標準,誰適合你的工廠?
急單、插單這種事,嗯,其實講白了,大多是因為供應鏈那邊節奏一緊,就連帶客戶需求也變得飄忽不定。唉,有時候真的很煩。然後全球市場現在都在吹什麼彈性生產的風潮,弄得企業根本喘不過氣。不過我突然想到昨天看到一則新聞,好像又跟這個沒太大關係……咦?好啦,拉回來。
說到地區管理風格,不知道是不是我太主觀,亞洲企業感覺特別重視團隊默契還有現場反應力,就是遇到突發狀況大家自己會互相cover一下;但歐美那邊嘛,他們比較死板(嗯,也許該說規範),偏愛標準流程,每件事資訊都公開透明,好壞各半吧。
欸,再聊資源配置,中大型集團畢竟底蘊深厚,可以專門拉出一個IT部門,全心全意推動那些新制(雖然員工有時候只想下班)。對比小型工廠就慘了,每次要試什麼新工具,都要左思右想,把投入跟回收率算到快冒煙才願意碰數位系統,他們就是謹慎到極點,有點猶豫也正常。
總之喔,要先搞清楚這些背景,免得哪天企業腦袋一熱照搬外面的方法進來,到頭來水土不服,一堆落差等著處理。啊,我是不是講太多了?其實…就是想提醒別人多想一步而已啦。
說到地區管理風格,不知道是不是我太主觀,亞洲企業感覺特別重視團隊默契還有現場反應力,就是遇到突發狀況大家自己會互相cover一下;但歐美那邊嘛,他們比較死板(嗯,也許該說規範),偏愛標準流程,每件事資訊都公開透明,好壞各半吧。
欸,再聊資源配置,中大型集團畢竟底蘊深厚,可以專門拉出一個IT部門,全心全意推動那些新制(雖然員工有時候只想下班)。對比小型工廠就慘了,每次要試什麼新工具,都要左思右想,把投入跟回收率算到快冒煙才願意碰數位系統,他們就是謹慎到極點,有點猶豫也正常。
總之喔,要先搞清楚這些背景,免得哪天企業腦袋一熱照搬外面的方法進來,到頭來水土不服,一堆落差等著處理。啊,我是不是講太多了?其實…就是想提醒別人多想一步而已啦。
IT人手少時,管理層如何決定升級腳步
嗯,前陣子去過幾間工廠,現場那個感覺我到現在還記得……他們那些產線啊,只要遇到插單,一口氣來好幾個,好吧,人力就這麼多。你想像一下,如果IT的人手又很有限,他們負責資料維護根本忙不過來,結果就變成資料更新慢半拍,甚至排程一亂起來更難搞,有時光是等資訊同步就頭大了。
然後,我有聽生管主管抱怨說,本來想導APS系統(對,就是那種Advanced Planning and Scheduling),但說真的啦,不太敢貿然上系統。因為大家都怕嘛——人工作業量突然暴增,誰受得了?搞不好還會出現一堆資訊斷層或誤判,而且壓力真的蠻爆表的。欸,其實講到這裡我自己也會擔心咧。回正題。
舉個例子好了——電子組裝產線吧,只要每日急單數累積、嗯,大概七十多單左右,你讓人員全手動處理?偏偏錯誤機率馬上飆高,再加上決策時間整個拖長,一堆東西卡在那邊就是進不去。有時候會忍不住問:他們怎麼沒先準備多點人?
所以囉,多數企業現在比較傾向什麼?他們通常會評估一下現有內部支援能量,看看到底能不能撐下去,不是一次性全部換掉,而是分階段慢慢來。例如先從高波動的產線做試點部署APS,希望可以先把初期衝擊跟資源消耗給分散一下。不過,也許有人會覺得這樣太保守,可……也只能一步步走嘛。
然後,我有聽生管主管抱怨說,本來想導APS系統(對,就是那種Advanced Planning and Scheduling),但說真的啦,不太敢貿然上系統。因為大家都怕嘛——人工作業量突然暴增,誰受得了?搞不好還會出現一堆資訊斷層或誤判,而且壓力真的蠻爆表的。欸,其實講到這裡我自己也會擔心咧。回正題。
舉個例子好了——電子組裝產線吧,只要每日急單數累積、嗯,大概七十多單左右,你讓人員全手動處理?偏偏錯誤機率馬上飆高,再加上決策時間整個拖長,一堆東西卡在那邊就是進不去。有時候會忍不住問:他們怎麼沒先準備多點人?
所以囉,多數企業現在比較傾向什麼?他們通常會評估一下現有內部支援能量,看看到底能不能撐下去,不是一次性全部換掉,而是分階段慢慢來。例如先從高波動的產線做試點部署APS,希望可以先把初期衝擊跟資源消耗給分散一下。不過,也許有人會覺得這樣太保守,可……也只能一步步走嘛。
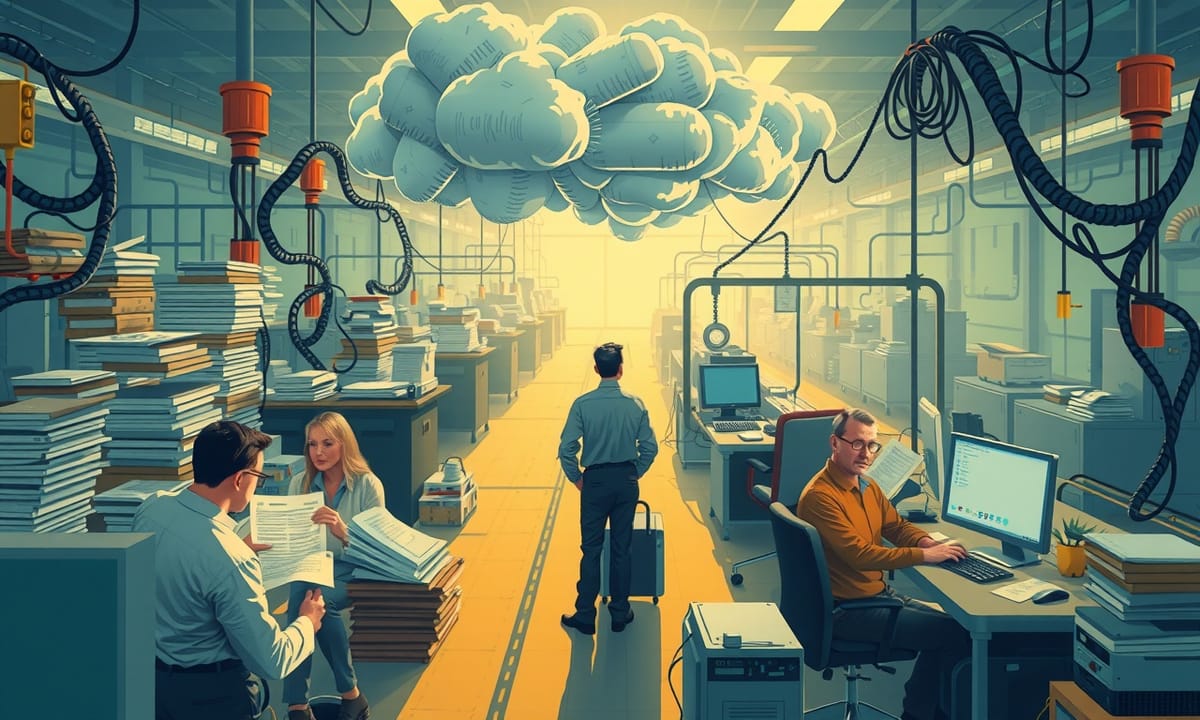
訂單達交率真的能衝頂?數據背後的迷霧
根據這幾年,不少國際研究機構做了關於製造業導入高級計畫排程(APS)的現場追蹤,嗯,結果其實挺一致的——訂單達交率本來大約八成,後來都提升到接近全滿,好像快沒什麼漏掉的。唉,有時候想一想,全滿到底是怎樣?反正就是大家數字都很漂亮啦。還有啊,那種急單處理,平均可以縮短好幾天,本來大家都以為只是宣傳用語,結果是真的能省下來。
說到人力資源調度,大部分企業講說整體規劃成本降幅有三成左右,其實這個數字聽起來很吸引人,可是我總覺得哪裡怪怪的……欸對,我剛剛想到昨天工廠裡又在抱怨加班。不過回主題,他們就是說三成嘛。有趣的是,只有將近一成五的專案最後完全達標,就是那種你原本期望什麼,它真的就做到什麼那種。主要卡住的地方還是在基礎資料蒐集不夠完整,以及部門之間資訊流通太慢,有時候等一個回報就拖半天。
另外也有一些顧問公司給建議,他們提倡連續三個月,每月至少三十筆急件記錄,由生管人員每天登打實際交貨縮短時間。其實我覺得這方法蠻土法煉鋼,但也貼近工廠日常狀態嘛。喔對了,我剛才差點忘記自己午餐還沒吃……呃拉回正題啦,就是透過這些細緻紀錄,可以比較精準評估APS系統在現場的真實效益,到底是不是像報告寫的一樣神奇。
說到人力資源調度,大部分企業講說整體規劃成本降幅有三成左右,其實這個數字聽起來很吸引人,可是我總覺得哪裡怪怪的……欸對,我剛剛想到昨天工廠裡又在抱怨加班。不過回主題,他們就是說三成嘛。有趣的是,只有將近一成五的專案最後完全達標,就是那種你原本期望什麼,它真的就做到什麼那種。主要卡住的地方還是在基礎資料蒐集不夠完整,以及部門之間資訊流通太慢,有時候等一個回報就拖半天。
另外也有一些顧問公司給建議,他們提倡連續三個月,每月至少三十筆急件記錄,由生管人員每天登打實際交貨縮短時間。其實我覺得這方法蠻土法煉鋼,但也貼近工廠日常狀態嘛。喔對了,我剛才差點忘記自己午餐還沒吃……呃拉回正題啦,就是透過這些細緻紀錄,可以比較精準評估APS系統在現場的真實效益,到底是不是像報告寫的一樣神奇。
引用來源:
- 先進規劃與排程系統 - MBA智库百科
Pub.: 2018-10-16 | Upd.: 2025-05-11 - APS是什麼?用APS打造高效、可持續的營運系統! | - 永續企業
Pub.: 2024-12-27 | Upd.: 2025-06-24 - iPASP APS 新一代智能規劃分析排程平台-
Pub.: 2025-05-27 | Upd.: 2025-06-16 - OLED製造廠先進規劃排程系統導入之研究
- 高级计划和排程(APS) 工具市场规模、份额、趋势[2032]
熬夜救火不再?現場焦慮與預防思維交鋒
「交期再拖下去怎麼辦?」這句話,嗯,幾乎每隔一段時間就會在會議桌上冒出來。坦白說,有時候我都想直接裝沒聽到,但腦袋又會自動跳回這個問題。急單的壓力像條沒人看得到的線,緊緊勒著所有管理層,不曉得你有沒有過那種感覺?現場主管,有些連夜還盯著手機訊息不放手,就是一直擔心啊,不是巴望早點把貨推出去,就是怕某個小細節突然爆了。
數據不是空穴來風——大約三成企業明明導入了自動化排程系統,可遇到突發訂單還是一樣亂成一團,好像每次都要重新學習一次怎麼滅火。有時候想,是不是基層人員反而比高層更希望系統能先預防狀況,而不是等東西炸掉才開始救場;嗯,我自己也有點搞不懂公司的期待到底在哪裡。
物料異動資訊,一份文件就得跨過幾個部門、蓋好幾層章才能落到產線,這流程本來就超容易卡關。啊,我剛剛想到昨天還有人抱怨被流程序困住,差點忘了主題,不扯遠——效率當然提不上來啦,都在跑流程。
有些公司現在開始重視即時資料回饋,比如生管每天都得上傳最新進度,碰上插單必須立刻提出備案。其實一開始大家都嫌麻煩死了,但日子久了,也漸漸習慣那種規律,似乎真的能多少減輕臨時狀況帶來的不安吧。
不過講到底,全靠工具是不行的。如果那些基礎資料老是缺東漏西,就算再好的系統,也只能補洞修網——彈性跟效率常常兩邊拉扯著,有時候真讓人懷疑,到底要選哪一頭才對。唉,有時人生就是這麼糾結吧。
數據不是空穴來風——大約三成企業明明導入了自動化排程系統,可遇到突發訂單還是一樣亂成一團,好像每次都要重新學習一次怎麼滅火。有時候想,是不是基層人員反而比高層更希望系統能先預防狀況,而不是等東西炸掉才開始救場;嗯,我自己也有點搞不懂公司的期待到底在哪裡。
物料異動資訊,一份文件就得跨過幾個部門、蓋好幾層章才能落到產線,這流程本來就超容易卡關。啊,我剛剛想到昨天還有人抱怨被流程序困住,差點忘了主題,不扯遠——效率當然提不上來啦,都在跑流程。
有些公司現在開始重視即時資料回饋,比如生管每天都得上傳最新進度,碰上插單必須立刻提出備案。其實一開始大家都嫌麻煩死了,但日子久了,也漸漸習慣那種規律,似乎真的能多少減輕臨時狀況帶來的不安吧。
不過講到底,全靠工具是不行的。如果那些基礎資料老是缺東漏西,就算再好的系統,也只能補洞修網——彈性跟效率常常兩邊拉扯著,有時候真讓人懷疑,到底要選哪一頭才對。唉,有時人生就是這麼糾結吧。
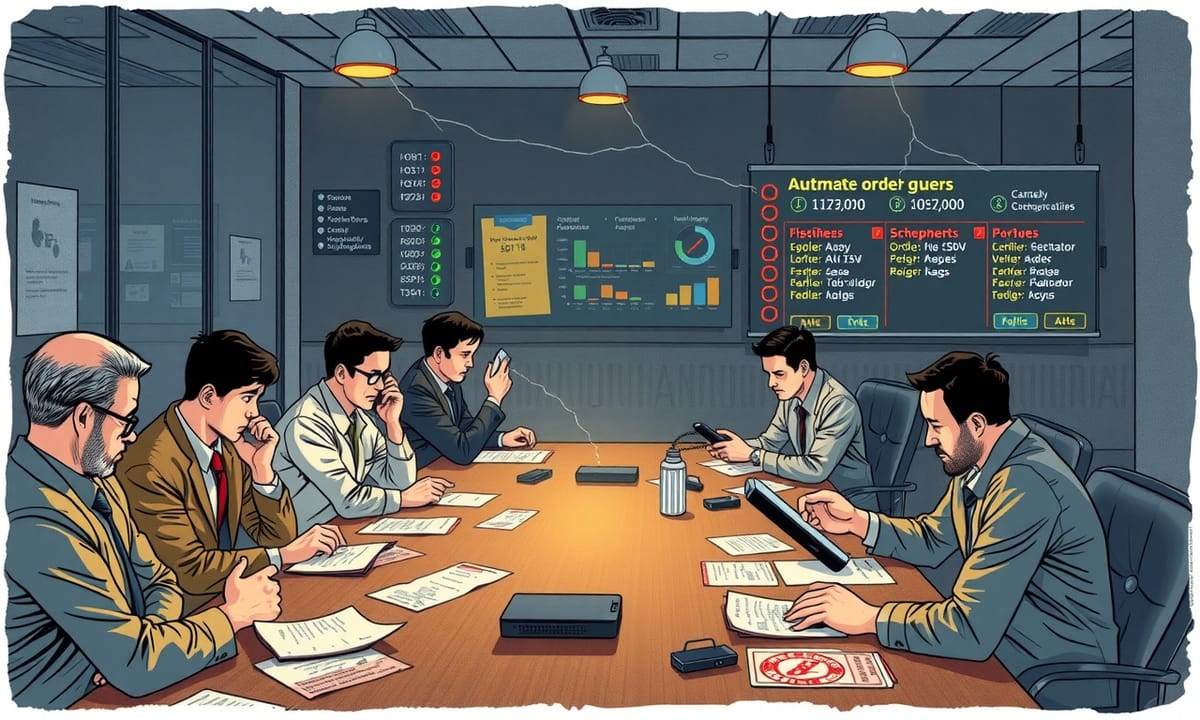
SaaS+IoT出奇制勝,小廠也有大作為瞬間
「我們以前插單就像在拆炸彈,」一個生管主管說的時候,臉上的苦笑都快寫進工廠裡頭了。「但現在流程順多了。」唉,想當年他們那套本地部署系統真是讓人頭痛,每次有插單消息傳來,全場跟踩到電線似的亂竄。這畫面我都還記得,有點荒謬又好笑。不過自從搭上雲端SaaS還有IoT設備監控之後,這種混亂大概少了一半吧。
每天他們用APS——嗯,就是那個高階排程系統啦,自動幫全廠把工單配置預演一次。然後領班會拿產線實際狀態和手邊的人員調度,再人工細修一輪確認,其實也不輕鬆,但速度真的快多了。有時候我會想,他們是不是晚上做夢也在調產線?扯遠了,總之這樣決策反應明顯變靈巧。
另外有家電子組裝廠,是直接把每日設備運轉數據即時丟到雲端平台去,然後用超簡易的儀表板檢查異常警示。欸,其實我自己對那些儀表板沒啥感覺,但現場工程師倒挺依賴,一發現潛在停機風險,就能提早排進明天計畫裡。突然想到,不知道他們午餐時間會不會也盯著那些警示燈發呆?
嗯,好像講太遠了。重點還是說,導入這些工具後,即使遇到將近一半插單量,也沒以前那麼慌張失序。生產節奏大致還撐得住,不至於全盤崩壞。有些人在現場說,只要懂得善用數據回饋、模擬排程,加強異常預警,人力再怎麼有限,也能打造比較不容易垮掉的營運流程——大抵如此吧。不過偶爾還是會有人碎念,那…啊算了,我又離題了。
每天他們用APS——嗯,就是那個高階排程系統啦,自動幫全廠把工單配置預演一次。然後領班會拿產線實際狀態和手邊的人員調度,再人工細修一輪確認,其實也不輕鬆,但速度真的快多了。有時候我會想,他們是不是晚上做夢也在調產線?扯遠了,總之這樣決策反應明顯變靈巧。
另外有家電子組裝廠,是直接把每日設備運轉數據即時丟到雲端平台去,然後用超簡易的儀表板檢查異常警示。欸,其實我自己對那些儀表板沒啥感覺,但現場工程師倒挺依賴,一發現潛在停機風險,就能提早排進明天計畫裡。突然想到,不知道他們午餐時間會不會也盯著那些警示燈發呆?
嗯,好像講太遠了。重點還是說,導入這些工具後,即使遇到將近一半插單量,也沒以前那麼慌張失序。生產節奏大致還撐得住,不至於全盤崩壞。有些人在現場說,只要懂得善用數據回饋、模擬排程,加強異常預警,人力再怎麼有限,也能打造比較不容易垮掉的營運流程——大抵如此吧。不過偶爾還是會有人碎念,那…啊算了,我又離題了。
設備保養沒跟上,再快排程也敵不過停機
多數時候,根據現場那些案例來看,把設備保養的資訊直接塞進每天的標準作業流程,好像就能擋住那種突如其來、讓人很想罵髒話的急單亂入。欸,其實細節還蠻多的喔,你得搞一個主檔資料自動更新機制,每天都要現場人員回報設備現在是活著還是快掛了,然後同步到APS平台——這裡有點煩,有時候網路又慢,不知道是不是只有我們遇到。嗯,另外系統要有例外事件通報欄位,一但臨時停機就馬上紀錄下來,不然之後根本追不到是哪台在鬧脾氣。
不過啊,有些東西光靠電腦死板板真的不行,所以系統最好給人工微調空間,例如領班可以照自己的經驗調整排程結果。這樣比較貼近現實吧?唉,我常覺得AI厲害歸厲害,但人的直覺有時候超難取代。不過也不能全靠感覺,比如說導入AI預警模組來找出潛在瓶頸,據說滿有效的。而且啊,把遇到的問題全丟進知識庫裡,以便之後優化流程,這聽起來雖然很理想,但整理起來總會拖延,不過總比亂成一團好。
至於怎麼推動嘛,行動面建議可以先拿部分產線測試,大概三個月觀察交期到底縮短沒,再慢慢往外擴。不敢一次全開,很怕剛上線就炸鍋。有趣的是,每次執行前大家都信誓旦旦,到第三週就有人喊累。反正,只要能降低初期推廣時踩雷風險,就算偷懶一下也沒什麼關係吧…。
不過啊,有些東西光靠電腦死板板真的不行,所以系統最好給人工微調空間,例如領班可以照自己的經驗調整排程結果。這樣比較貼近現實吧?唉,我常覺得AI厲害歸厲害,但人的直覺有時候超難取代。不過也不能全靠感覺,比如說導入AI預警模組來找出潛在瓶頸,據說滿有效的。而且啊,把遇到的問題全丟進知識庫裡,以便之後優化流程,這聽起來雖然很理想,但整理起來總會拖延,不過總比亂成一團好。
至於怎麼推動嘛,行動面建議可以先拿部分產線測試,大概三個月觀察交期到底縮短沒,再慢慢往外擴。不敢一次全開,很怕剛上線就炸鍋。有趣的是,每次執行前大家都信誓旦旦,到第三週就有人喊累。反正,只要能降低初期推廣時踩雷風險,就算偷懶一下也沒什麼關係吧…。
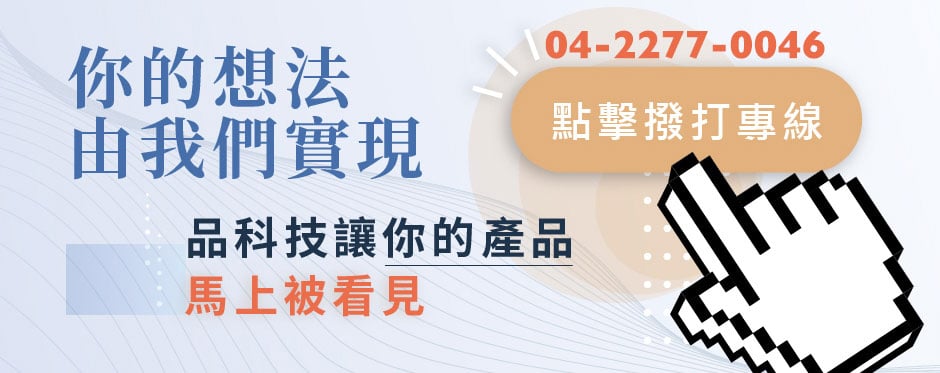