核心行動建議 - 幫助工廠快速落實高效排程,減少待料與出貨延誤
- 定期檢查設備與模具狀況,每周盤點生產線主要機台健康度。
提前發現異常可降低臨時停機風險,避免生產中斷造成延遲。
- 優先安排同模具、同材料訂單連續排產,換模次數每班不超過2次。
降低切換損耗,一週能多省下10%以上的工時和材料浪費。
- 每月針對資訊流通進行短會檢討,追蹤關鍵訊息回報是否在24小時內完成。
縮短決策等待時間,有效減少內部溝通漏接導致的誤會與失誤。
- *建立持續回饋管道*,每季收集現場人員改善意見不少於5則並採納1項以上。
*一線經驗直接轉化為優化方案,有助提升系統適應性及團隊認同感。*
盲目追數位?還是先想內部適應門檻
自動化設備和那些所謂的智慧系統,嗯,最近幾年好像到處都在講——全球的工廠現場正慢慢被這些東西佔據。你走進一間傳產公司,也許還能聞到油味,可是其實他們很多早就開始摸索數位科技了,大概想靠生產力工具、智能排程什麼的,把效率和彈性問題丟給機器人解決。說真的,我有時會懷疑那台機械臂懂不懂我們壓力在哪。
欸,有點離題。拉回來講,其實這波數位轉型也不是哪個地區獨享啦。不論是歐美那種所謂成熟市場,還是亞洲新興工業帶,都很熱衷,而且不分大品牌或小零組件供應商,好像誰沒跟上就會被甩開似的。有份研究…唉,我忘了是哪家,但內容倒記得——將近一半受訪製造公司說他們在考慮導入先進資訊技術,聽起來很威風對吧?可是一旦要真正落地,就冒出流程銜接斷層、團隊適應卡關之類狀況。
總之噢,即使自動化或者MES(製造執行系統)方案成為大家搶著談的新寵兒,各地現場推展狀態還是差很大。有些地方跑得快,有些乾脆原地踏步。所以最後啊,也只能根據每個情境去看它們到底有沒有發揮預期效益。嗯,大致就是這樣吧。我是不是又碎念太多?
欸,有點離題。拉回來講,其實這波數位轉型也不是哪個地區獨享啦。不論是歐美那種所謂成熟市場,還是亞洲新興工業帶,都很熱衷,而且不分大品牌或小零組件供應商,好像誰沒跟上就會被甩開似的。有份研究…唉,我忘了是哪家,但內容倒記得——將近一半受訪製造公司說他們在考慮導入先進資訊技術,聽起來很威風對吧?可是一旦要真正落地,就冒出流程銜接斷層、團隊適應卡關之類狀況。
總之噢,即使自動化或者MES(製造執行系統)方案成為大家搶著談的新寵兒,各地現場推展狀態還是差很大。有些地方跑得快,有些乾脆原地踏步。所以最後啊,也只能根據每個情境去看它們到底有沒有發揮預期效益。嗯,大致就是這樣吧。我是不是又碎念太多?
出貨延誤背後的待料連鎖效應
「現場待料狀況幾乎每天都在上演,」某個資深製造業主管最近跟我說這句話時,臉色有點無奈。其實這種困境……怎麼講,說穿了不只是什麼進度落後、數字不好看這麼簡單而已,更麻煩的是它直接影響到營運成本,還會讓客戶的信任感一點一滴消磨掉。唉,光想就覺得頭痛。
那天聽完幾次產線訪談,發現將近一半的管理者坦白講,其實排程老是失效最大的問題還是在於物料資訊根本沒辦法及時更新。嗯,我有時候也在想,是不是人手真的不夠?但他們又說部門之間協作環節反應不夠靈敏也是主因之一。結果呢?只要某個零件稍微沒跟上、生產瓶頸訊息傳遞又慢半拍,「待料」這三個字就像骨牌一樣,一路從前端拖到最終出貨;想到這裡腦袋開始亂飄——啊對,剛才還差點忘了。
有些企業會自豪說已經導入MES或者其他自動化系統,可是實際現場如果資訊還是斷層,再怎麼厲害的工具,其實也避免不了延誤。好吧,有時候真的很想問,到底要怎麼解決?這類問題總算提醒我們,如果管理層真心想處理生產現場兩大痛點,需要的不只是軟體系統(嗯,不用再強調科技多先進),反而該是全流程透明且可追溯的協作機制才行,大概吧。
那天聽完幾次產線訪談,發現將近一半的管理者坦白講,其實排程老是失效最大的問題還是在於物料資訊根本沒辦法及時更新。嗯,我有時候也在想,是不是人手真的不夠?但他們又說部門之間協作環節反應不夠靈敏也是主因之一。結果呢?只要某個零件稍微沒跟上、生產瓶頸訊息傳遞又慢半拍,「待料」這三個字就像骨牌一樣,一路從前端拖到最終出貨;想到這裡腦袋開始亂飄——啊對,剛才還差點忘了。
有些企業會自豪說已經導入MES或者其他自動化系統,可是實際現場如果資訊還是斷層,再怎麼厲害的工具,其實也避免不了延誤。好吧,有時候真的很想問,到底要怎麼解決?這類問題總算提醒我們,如果管理層真心想處理生產現場兩大痛點,需要的不只是軟體系統(嗯,不用再強調科技多先進),反而該是全流程透明且可追溯的協作機制才行,大概吧。
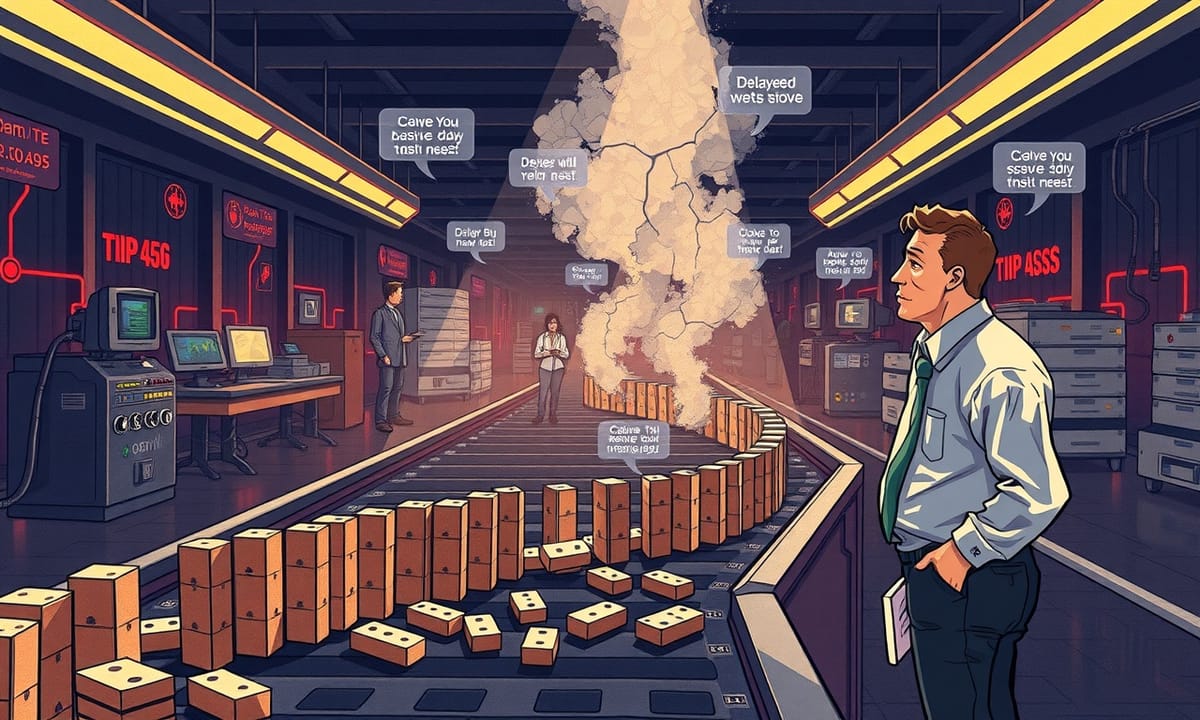
資訊流通慢,企業損耗其實無聲發生
根據工研院在二〇二三年針對台灣製造業現場做的調查,老實說,我有點意外——傳統手動排程,資訊流通不即時居然還是常見狀況。嗯,是這樣啦:生產線待料、停工什麼的,其實都還滿令人煩躁。如果以金屬加工廠來舉例好了,當他們導入智慧工廠模組之後,嘿,生產效率硬生生提升了將近兩成。這數字看起來很亮眼嘛,同時間也把停機時間跟稽核成本往下壓了一把(來源:[2])。
唉我突然想到上次經過某家工廠門口,那機器聲好吵,但拉回正題——這些數據老實說反映得很清楚。如果部門間資訊更新速度太慢,又追不上現場需求,不但會讓工單週轉拖得更久,有時候還會因為一連串誤差堆疊出一堆隱形損耗。欸對,多項研究觀察都有提到,每次只要物料到位或者訊息傳遞延遲超過幾個小時,整條產線裡那些非必要等待就莫名地明顯增加起來。不知道你有沒有碰過那種「等一下」永遠沒消失的情境?最後對經理人來說,就算只有七十多分鐘的資訊落差,到頭來年度結算那天竟然能膨脹成數十倍的人力或設備資源浪費——嗯,大概就是這麼誇張吧。
唉我突然想到上次經過某家工廠門口,那機器聲好吵,但拉回正題——這些數據老實說反映得很清楚。如果部門間資訊更新速度太慢,又追不上現場需求,不但會讓工單週轉拖得更久,有時候還會因為一連串誤差堆疊出一堆隱形損耗。欸對,多項研究觀察都有提到,每次只要物料到位或者訊息傳遞延遲超過幾個小時,整條產線裡那些非必要等待就莫名地明顯增加起來。不知道你有沒有碰過那種「等一下」永遠沒消失的情境?最後對經理人來說,就算只有七十多分鐘的資訊落差,到頭來年度結算那天竟然能膨脹成數十倍的人力或設備資源浪費——嗯,大概就是這麼誇張吧。
引用來源:
- 如何有效進行「跨部門溝通」?掌握這5大技巧,讓溝通無界限
Pub.: 2024-05-13 | Upd.: 2025-06-16 - 部门间协作为何失败? - TPP智管理系统
Pub.: 2024-12-01 | Upd.: 2024-12-26 - 何謂智慧製造?從數據應用到黑燈工廠,中小企業也能有效提升生產 ...
Pub.: 2024-11-14 | Upd.: 2025-06-12 - [PDF] 智慧國家方案(2021-2025年)
- 提升跨部溝通與異議協調運用實務班 - 中華工商研究院
Pub.: 2025-01-01 | Upd.: 2025-03-22
制度建了卻卡溝通,人性因素更頑強
「系統再怎麼換,好像都一樣,唉。」這種話我也常聽到,尤其車間裡面,大家偶爾就嘆口氣冒出來,說真的,也不確定他們是認真還是單純無力感吧。部門之間隔了好幾層牆,一層又一層,有時候你拼命講規章制度、一直重複,可總有些人硬是不走那條大道,就是要自己繞個圈。欸,我是不是說遠了?嗯,拉回來——有些現場頭頭就是只信自己的經驗,不管流程寫得多細緻,他們只挑符合自己習慣的做法。
新工具裝進去也沒什麼神奇魔法啦,其實資訊孤島這東西不是什麼舊企業才會遇到的怪獸,新廠區照樣難逃一劫。有時候明明上面的指令下得很快,可底下的人反應總慢半拍,大概大家都有點拖延症?跨單位合作也是,每次提到「這不是我的範圍喔」,推來推去,到最後整個界線霧成一團。一但發生哪怕微小變動,就沒有人想揹鍋,那誰願意承擔啊!結果每個環節都卡住、追查問題連源頭都找不到。
表面看起來嘛——規劃圖很漂亮,好像一切井然,但內部卻充滿那種溝通的小摩擦,只要沒處理妥當,再厲害的新系統也只是換個介面在騙自己罷了。有時候我會懷疑,是不是人跟制度之間那些夾雜不清的細碎矛盾,其實才讓排程亂象永遠原地打轉?大概如此吧。
新工具裝進去也沒什麼神奇魔法啦,其實資訊孤島這東西不是什麼舊企業才會遇到的怪獸,新廠區照樣難逃一劫。有時候明明上面的指令下得很快,可底下的人反應總慢半拍,大概大家都有點拖延症?跨單位合作也是,每次提到「這不是我的範圍喔」,推來推去,到最後整個界線霧成一團。一但發生哪怕微小變動,就沒有人想揹鍋,那誰願意承擔啊!結果每個環節都卡住、追查問題連源頭都找不到。
表面看起來嘛——規劃圖很漂亮,好像一切井然,但內部卻充滿那種溝通的小摩擦,只要沒處理妥當,再厲害的新系統也只是換個介面在騙自己罷了。有時候我會懷疑,是不是人跟制度之間那些夾雜不清的細碎矛盾,其實才讓排程亂象永遠原地打轉?大概如此吧。
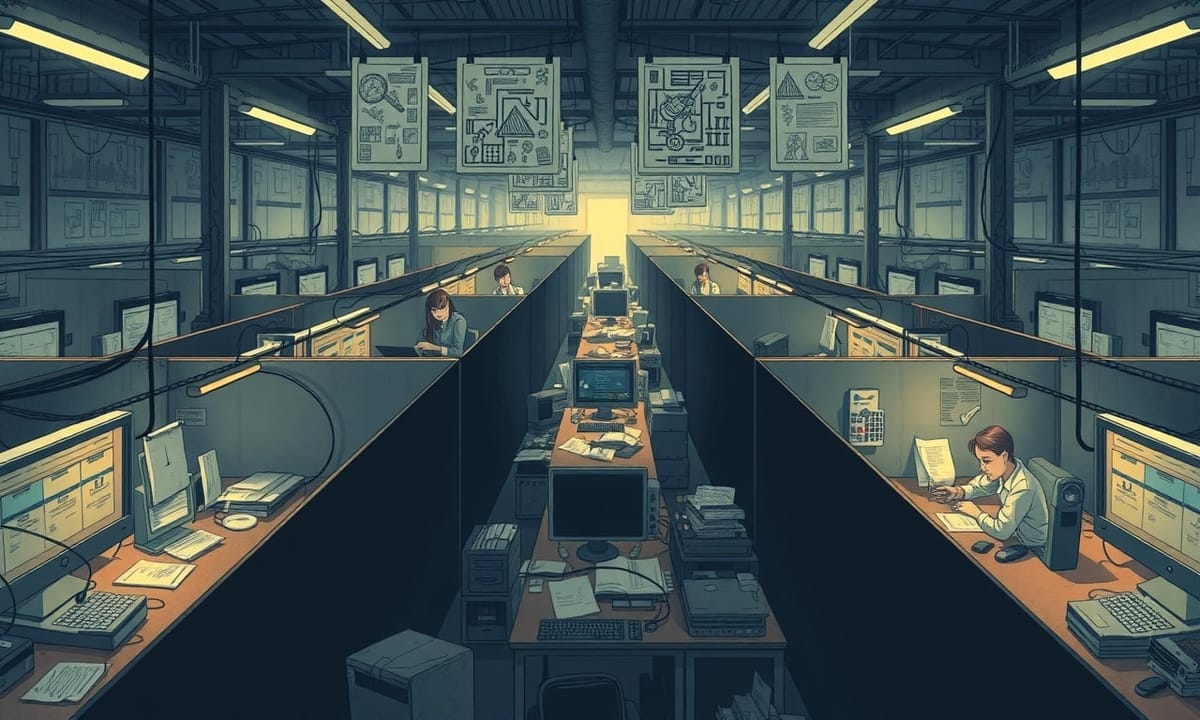
軟體不是萬靈丹,需求盤點才是根本
「你如果只想靠現有表單直接搬進新系統,幾乎都會碰上水土不服。」嗯,這句話很刺耳,但業界顧問就是講得這麼直白。其實也不是大家懶啦,只要省掉需求盤點或是懶得重整流程,導入下去後權限設計亂七八糟、待料狀態一團迷霧、跨部門資訊卡在半路——反正問題多到數不清。唉,有時候我也搞不懂,為什麼這種事每次都還是會重演。
以製造業來看好了,最近中小企業瘋狂引進那種打著自動化名號的排程平台,可惜啊,他們沒空仔細梳理物料流向跟各崗位到底誰負責哪一段。結果怎樣?紙本上的困境只是被拷貝到螢幕裡罷了,多了一層視窗切換的無力感。對了,我昨天還看到某家廠商居然用 Excel 管全部工序,不知道該哭還笑。
所以啊,如果真的想做對,就應該站在所有使用者角度慢慢釐清作業邏輯。有沒有先明訂哪些人能異動關鍵資料?再設定自動提醒機制?嗯……結果常常跳過這些環節。同時要把教育訓練納入排程計畫裡面,但老實說,好像沒幾間公司願意花時間做全套。我自己以前受訓時就總覺得,一堆同事根本沒聽進去。
磨合期太短,大約七成員工最後只學會最表層功能吧,其實反而降低原本預期的改善效果。有趣的是,那些跨部門回饋管道,看起來只是雞毛蒜皮的小細節,可是在後續維運階段往往決定系統推行能不能走下去。不知道是不是只有我覺得,每次推新東西最後都變成少數人在撐場面……好吧,又扯遠了。
以製造業來看好了,最近中小企業瘋狂引進那種打著自動化名號的排程平台,可惜啊,他們沒空仔細梳理物料流向跟各崗位到底誰負責哪一段。結果怎樣?紙本上的困境只是被拷貝到螢幕裡罷了,多了一層視窗切換的無力感。對了,我昨天還看到某家廠商居然用 Excel 管全部工序,不知道該哭還笑。
所以啊,如果真的想做對,就應該站在所有使用者角度慢慢釐清作業邏輯。有沒有先明訂哪些人能異動關鍵資料?再設定自動提醒機制?嗯……結果常常跳過這些環節。同時要把教育訓練納入排程計畫裡面,但老實說,好像沒幾間公司願意花時間做全套。我自己以前受訓時就總覺得,一堆同事根本沒聽進去。
磨合期太短,大約七成員工最後只學會最表層功能吧,其實反而降低原本預期的改善效果。有趣的是,那些跨部門回饋管道,看起來只是雞毛蒜皮的小細節,可是在後續維運階段往往決定系統推行能不能走下去。不知道是不是只有我覺得,每次推新東西最後都變成少數人在撐場面……好吧,又扯遠了。
績效壓力下的現場真相與自主平衡
「數位化管理不等於監控失衡。」這句話——嗯,說得有點重?不過確實有人直接指出來。製造現場開始弄什麼自動進度追蹤、KPI設計,一線人員倒也不是完全反對啦,他們其實還挺樂意看到流程變透明、查核方便。可是那種績效指標,如果細緻到每一個小環節都要被盯著,好像也會壓力大到爆炸。這我真的懂,有時候想到就頭痛。
唉,其實產業論壇最近在討論這事,大約有一半顧問(不是亂講,真的是將近一半)都認為,自動化如果沒有正向回饋或彈性調整的機制,士氣很容易滑落谷底。有些公司推全自動工序記錄——欸,我突然想起上次開會時差點睡著——他們只管差異比對啊、即時警示啊,卻忘了鼓勵達標和創新的人,結果是什麼?前線員工後來都很佛系地應付,反正被盯久了誰還有心情玩命。
然後,相較之下,也有一些廠商比較聰明吧?他們除了那些硬梆梆的追蹤工具外,也會同步搞個心理安全回饋窗口,再加上一些彈性的介入制度。奇怪,就是因為多做這點事情,他們成效能維持住,不容易掉鍊子,而且抗拒的情緒好像也減輕不少。嗯……看起來,就算再怎麼愛效率,有時候也得給人喘口氣才行吧。
唉,其實產業論壇最近在討論這事,大約有一半顧問(不是亂講,真的是將近一半)都認為,自動化如果沒有正向回饋或彈性調整的機制,士氣很容易滑落谷底。有些公司推全自動工序記錄——欸,我突然想起上次開會時差點睡著——他們只管差異比對啊、即時警示啊,卻忘了鼓勵達標和創新的人,結果是什麼?前線員工後來都很佛系地應付,反正被盯久了誰還有心情玩命。
然後,相較之下,也有一些廠商比較聰明吧?他們除了那些硬梆梆的追蹤工具外,也會同步搞個心理安全回饋窗口,再加上一些彈性的介入制度。奇怪,就是因為多做這點事情,他們成效能維持住,不容易掉鍊子,而且抗拒的情緒好像也減輕不少。嗯……看起來,就算再怎麼愛效率,有時候也得給人喘口氣才行吧。
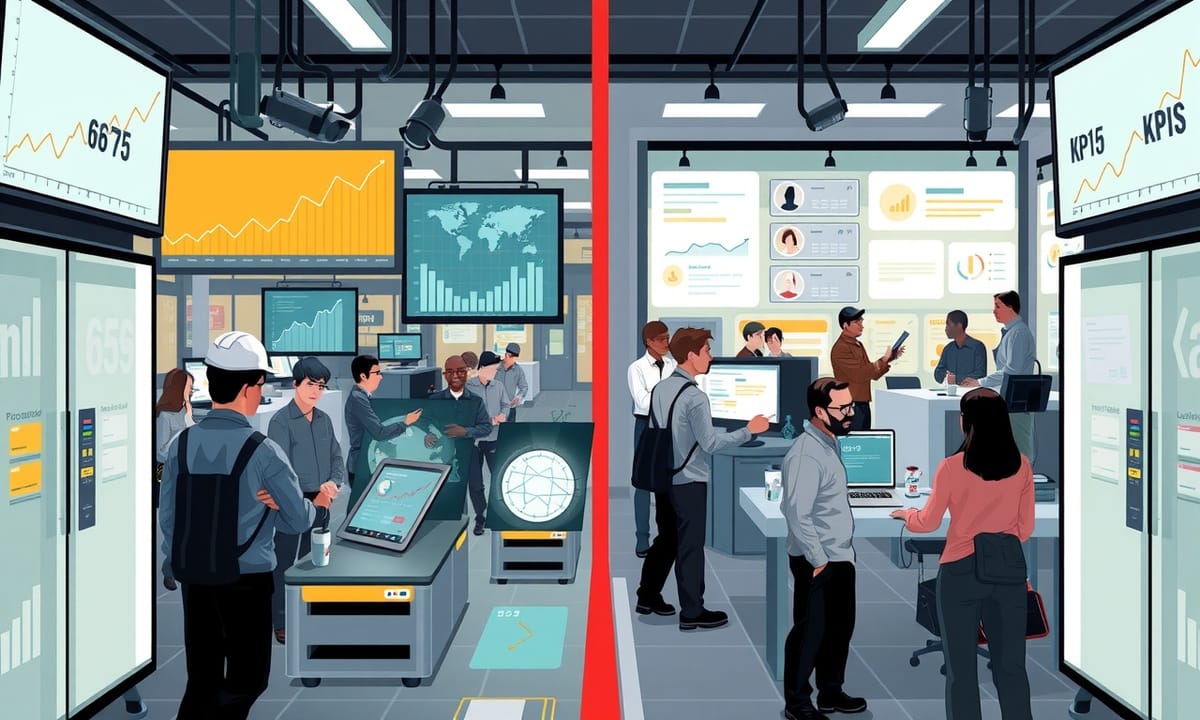
七步驟不亂來:從瓶頸找回真問題
有時候,廠商總以為只要買一套系統回來,生產瓶頸馬上就能被解決掉。嗯,現實真不是這麼單純。其實,根據台灣製造業這幾年的導入經驗(我真的有聽過不少案例),真正有效的作法往往得拆成七個步驟才行。第一步——一定得先抓出最關鍵、讓人生氣的那個瓶頸,到底是訂單老是延遲呢?還是那些設備整天閒在那邊發呆?唉,每次討論都會有人說「都很重要」,但不挑出來最後什麼也沒解決。
然後啊,還得收集原始數據,不是隨便記幾筆就好。例如你可能要挑選某一個月內,大約五十筆訂單,把『待料總小時』這種細節記錄下來。有點瑣碎吧,但這步驟跳過真的後面會亂成一團。我自己以前也是懶過,不過最後還是乖乖地補資料。
下一階段嘛,就是規劃跨部門協作路徑啦,不然資訊永遠卡死在同一個人手裡。講到這我突然想到,上次開會某主管直接消失兩天……好啦拉回主題,只要協作流程順了,很多問題就不會再反覆出現。
再來必須建立快速的回饋迴圈,同時間安排教育訓練,不然新流程推動起來就是卡住。其實每次訓練大家表面上都有聽進去,可是真的落實下去又是一回事,我自己也常常覺得疑惑:到底誰真的照做了?
接著,就只能持續定期檢討優化細節,有些看似微不足道的小地方,結果卻大幅提升效率。欸對了,有時候檢討會突然變成吐槽大會……呃,不重要啦,反正就是別停下修正腳步。
最後,要設計追蹤機制,好讓改善幅度能夠被逐步驗證,而不是大家拍胸脯說「有進步」就算數。不然投入資源搞半天,只做做樣子,那真的是白忙一場,大概沒人想看到吧。
然後啊,還得收集原始數據,不是隨便記幾筆就好。例如你可能要挑選某一個月內,大約五十筆訂單,把『待料總小時』這種細節記錄下來。有點瑣碎吧,但這步驟跳過真的後面會亂成一團。我自己以前也是懶過,不過最後還是乖乖地補資料。
下一階段嘛,就是規劃跨部門協作路徑啦,不然資訊永遠卡死在同一個人手裡。講到這我突然想到,上次開會某主管直接消失兩天……好啦拉回主題,只要協作流程順了,很多問題就不會再反覆出現。
再來必須建立快速的回饋迴圈,同時間安排教育訓練,不然新流程推動起來就是卡住。其實每次訓練大家表面上都有聽進去,可是真的落實下去又是一回事,我自己也常常覺得疑惑:到底誰真的照做了?
接著,就只能持續定期檢討優化細節,有些看似微不足道的小地方,結果卻大幅提升效率。欸對了,有時候檢討會突然變成吐槽大會……呃,不重要啦,反正就是別停下修正腳步。
最後,要設計追蹤機制,好讓改善幅度能夠被逐步驗證,而不是大家拍胸脯說「有進步」就算數。不然投入資源搞半天,只做做樣子,那真的是白忙一場,大概沒人想看到吧。
預算小也能做,低成本排程優化路線圖
「訂單十天內有七成變動,排程每天都重來一次,」台中工業區那家機械零件廠的經理說這話時,一臉茫然。其實我聽了也不太確定,怎麼會這樣。原本他們靠手抄白板還有Excel輪班協作,有點復古又無奈。有時候供應延誤,全場只能發呆,不知道該幹嘛。唉,有些日子物料卡在倉庫半天沒人查覺,好像大家都自顧不暇。
後來,他們試著用很陽春的MES把現有Excel串起來,設計出一份土土的「待料警示表」。欸,我先岔個題,如果是我的話大概會偷懶直接不理——但他們挺認真的,每次只要訂單哪裡出現異常狀況,大概三小時內負責人就能收到通知,也算快吧。不過這種半自動化方法,其實功能也很有限,但至少讓管理層開始看得清楚,到底是哪幾個品項總是在拖延;你知道嗎,還能反查是哪道程序扯後腿。
講真的,他們抓了將近五十份最近問題特別多的出貨紀錄,一邊記錄待料時間,一邊比對人工與系統安排下差多少——嗯,那落差數字還真明顯。結果只是針對短期高波動訂單微調規則,就讓等待物料的總時數少掉約三成。我突然想到隔壁那間傳統工廠依然「先來先做」萬年不變,那效率……算了,不提也罷。欸,看起來沒花什麼額外費用,人家就已經開始整理瓶頸線索。
至於全自動設備?經理搖頭:「條件根本不允許,不如先把自己搞懂。」我每次聽到這種回答都有點想笑又佩服,畢竟不是誰都受得了把複雜東西拆開從頭摸索一遍吧。
後來,他們試著用很陽春的MES把現有Excel串起來,設計出一份土土的「待料警示表」。欸,我先岔個題,如果是我的話大概會偷懶直接不理——但他們挺認真的,每次只要訂單哪裡出現異常狀況,大概三小時內負責人就能收到通知,也算快吧。不過這種半自動化方法,其實功能也很有限,但至少讓管理層開始看得清楚,到底是哪幾個品項總是在拖延;你知道嗎,還能反查是哪道程序扯後腿。
講真的,他們抓了將近五十份最近問題特別多的出貨紀錄,一邊記錄待料時間,一邊比對人工與系統安排下差多少——嗯,那落差數字還真明顯。結果只是針對短期高波動訂單微調規則,就讓等待物料的總時數少掉約三成。我突然想到隔壁那間傳統工廠依然「先來先做」萬年不變,那效率……算了,不提也罷。欸,看起來沒花什麼額外費用,人家就已經開始整理瓶頸線索。
至於全自動設備?經理搖頭:「條件根本不允許,不如先把自己搞懂。」我每次聽到這種回答都有點想笑又佩服,畢竟不是誰都受得了把複雜東西拆開從頭摸索一遍吧。
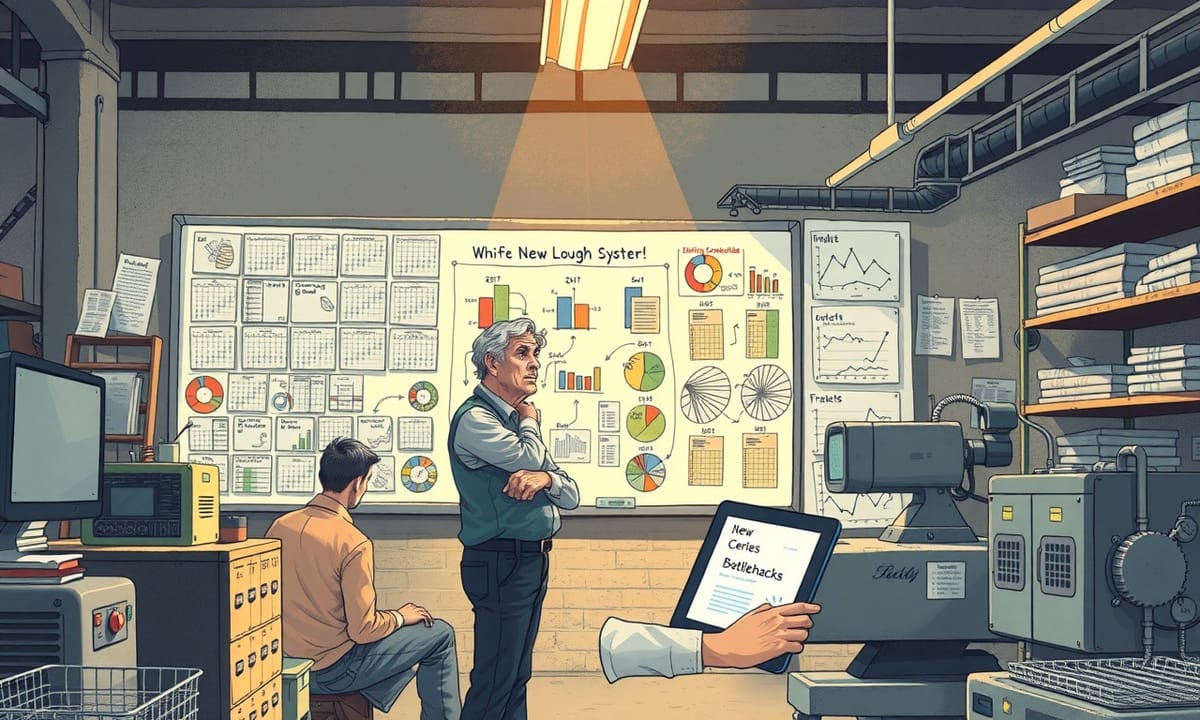
自動化系統風險:指標美但漏洞多?
「自動化系統不會出錯」這種說法,嗯,其實現場狀況就早已打臉了。還記得疫情剛爆發那時,有企業試著用演算法來做排程,聽起來很炫,但他們沒注意到,人力變動和供應延遲的資料根本沒跟上修正。結果怎麼樣呢?生產計畫一改再改,唉,損失竟然被放大數十倍,好像愈自信反而踩更多坑。有時管理層眼裡只剩下系統吐出來那些漂亮指標,可底層輸入如果有錯誤,又遇到什麼突發異常,你要溯源其實超難。
欸,我是不是又扯遠了?不過說真的,缺乏即時判斷或異常分析的能力,自動化反倒變成風險擴大的推手。人嘛,有時總想偷懶全交給機器處理,但你看這些例子後,大概會明白,每個關鍵決策環節都還是得保留人工審視、主動查核,不然一旦出了岔,就只能無助地看著黑盒運作繼續出包——講到這裡忽然有點悶,不過也只能繼續拉回主題吧。
欸,我是不是又扯遠了?不過說真的,缺乏即時判斷或異常分析的能力,自動化反倒變成風險擴大的推手。人嘛,有時總想偷懶全交給機器處理,但你看這些例子後,大概會明白,每個關鍵決策環節都還是得保留人工審視、主動查核,不然一旦出了岔,就只能無助地看著黑盒運作繼續出包——講到這裡忽然有點悶,不過也只能繼續拉回主題吧。
彈性排程未來式,韌性運營才撐得久
現場的經驗,大多啦,都是摸著石頭過河這樣。你要建立一個彈性又能即時反應的排程體系,其實說穿了,最關鍵還是「快速回饋」和所謂「跨部門共創規則」。嗯,有點像玩團體遊戲吧,不過這話講得好抽象。啊,等等我想起來,有家企業,他們就很簡單,用MES搭配Excel記錄那幾十筆訂單——好像也不是什麼高深科技——結果只開啟部分自動化功能,竟然待料時間就明顯縮短了,好神奇欸。
先說步驟好了。首先,你得抓出最大瓶頸是哪裡;唉,很多人會跳過這一步直接亂搞——真的別學他們。接下來,就是蒐集原始資料,例如每日待料總時數那些瑣碎但重要的數據。不知道為什麼,每次整理都有人喊累,但沒辦法嘛,要推進事情就是得有耐心。
再來啊,要設計一個平台,不光只是美其名讓不同部門能參與設定優先順序,更重要的是大家願意輪流拉回討論焦點,不然常常聊著聊著就偏題。每週調整、反饋流程也一定要落地,不要只在PPT上畫大餅。我自己有時候都覺得麻煩,可是真的需要。
選擇系統時最好找那種規則可以彈性調整、又能處理例外狀況的。其實啊,只靠演算法滿腦子自動運算,也容易忽略異常分析,最後現場一亂全盤皆輸。我有一次差點踩雷,所以特別有感。這類做法,可以慢慢消弭資訊孤島或太死板規範帶來的混亂。而且咦,就算設備條件有限,只要肯花時間打磨流程,也還是能逐步提升運營韌性吧,大概是這樣啦。
先說步驟好了。首先,你得抓出最大瓶頸是哪裡;唉,很多人會跳過這一步直接亂搞——真的別學他們。接下來,就是蒐集原始資料,例如每日待料總時數那些瑣碎但重要的數據。不知道為什麼,每次整理都有人喊累,但沒辦法嘛,要推進事情就是得有耐心。
再來啊,要設計一個平台,不光只是美其名讓不同部門能參與設定優先順序,更重要的是大家願意輪流拉回討論焦點,不然常常聊著聊著就偏題。每週調整、反饋流程也一定要落地,不要只在PPT上畫大餅。我自己有時候都覺得麻煩,可是真的需要。
選擇系統時最好找那種規則可以彈性調整、又能處理例外狀況的。其實啊,只靠演算法滿腦子自動運算,也容易忽略異常分析,最後現場一亂全盤皆輸。我有一次差點踩雷,所以特別有感。這類做法,可以慢慢消弭資訊孤島或太死板規範帶來的混亂。而且咦,就算設備條件有限,只要肯花時間打磨流程,也還是能逐步提升運營韌性吧,大概是這樣啦。
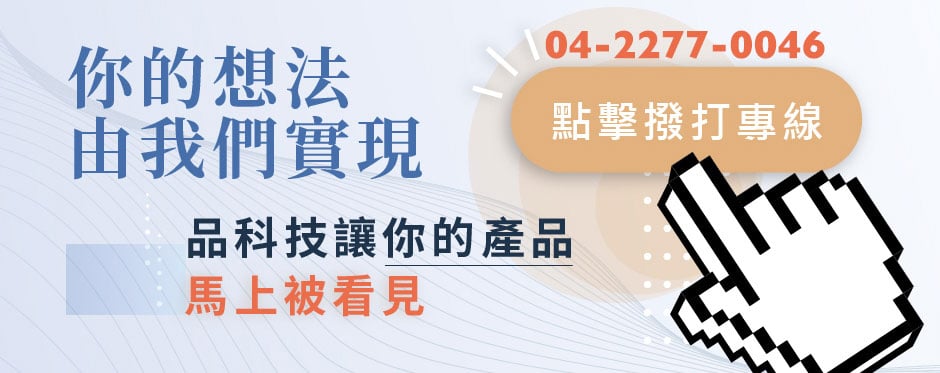