核心行動建議 - 提供可撓性 OLED 技術與市場應用的實務操作指引,助力企業把握新興商機並降低技術風險
- 定期執行彎折循環測試,確保產品在10000次以上彎折後仍維持穩定性能
可有效預防因輕薄設計帶來的材料疲勞和壽命縮短問題
- 鎖定供應鏈中具備垂直整合能力的廠商,以確保原料到封裝各階段品質控制達標
能減少跨域協同瓶頸,加快量產速度並降低總成本
- 採用混合方案搭配模組拆裝思維,在預算限制內優化面板性能與維修便利性
提升產品競爭力,同時降低後期維護門檻及成本負擔
- 建立長周期亮度及老化監控系統,每月至少收集一次現場數據作為參考依據
"有助於掌握材料劣化趨勢,提前調整製程或設計以延長使用壽命"
從mini測試到量產驗證:可撓OLED的每一步檢查
最近看產業新聞,發現柔性有機發光二極體(反正大家也叫它可撓式OLED啦)好像已經慢慢從實驗室走到真正能賣錢的地方了。有時候想,技術進步到底是快還是慢呢?嗯,不扯遠。你如果要把資源丟進這種新東西,最先得盤點自己要用在哪——比方說拿去做車載顯示器,還是醫療監測設備?說真的,它們對耐用性和穩定度的要求都高得不像話,比那些一般消費型小玩意兒麻煩多了。
唉,其實我常常想這些標準是不是太嚴格,不過回頭看,好像沒辦法鬆綁。然後啊,針對不同的垂直市場,他們通常會組個跨部門專案小組,把工程、產品設計、產線管理的人全部拉在一起討論。欸,我突然想到上次開會時大家互相推皮球,結果差點沒吵起來。不過主題還是回來講——這些人會一起評估應用現場遇到的問題,比如溫濕度變化啦、外力衝擊什麼的,有夠瑣碎。
最後嘛,有個建議就是可以預留一部分研發資源給現場回饋跟快速調整用。我有時候覺得現場人員才是真正懂狀況的人。當然,也不是每次都能如願調整那麼快,但至少這樣弄下來,可以讓解決方案更貼近終端實際情境,用起來順手多了。嗯,大概就是有助於之後導入效率和成果穩定吧。其實寫到這邊我都有點累了,不過細節真的不得不提啊。
唉,其實我常常想這些標準是不是太嚴格,不過回頭看,好像沒辦法鬆綁。然後啊,針對不同的垂直市場,他們通常會組個跨部門專案小組,把工程、產品設計、產線管理的人全部拉在一起討論。欸,我突然想到上次開會時大家互相推皮球,結果差點沒吵起來。不過主題還是回來講——這些人會一起評估應用現場遇到的問題,比如溫濕度變化啦、外力衝擊什麼的,有夠瑣碎。
最後嘛,有個建議就是可以預留一部分研發資源給現場回饋跟快速調整用。我有時候覺得現場人員才是真正懂狀況的人。當然,也不是每次都能如願調整那麼快,但至少這樣弄下來,可以讓解決方案更貼近終端實際情境,用起來順手多了。嗯,大概就是有助於之後導入效率和成果穩定吧。其實寫到這邊我都有點累了,不過細節真的不得不提啊。
全球供應鏈角力下,誰主柔性面板市場新賽局?
國際市場研究機構這幾年分析了一下,汽車顯示相關的需求…嗯,真的是一直往上衝啊。反正現在誰還會質疑這一塊不熱?說真的,已經成為柔性OLED產業發展的一股很難忽視的力量。說到豪華車廠,他們不都很愛找那種設計彈性又視覺效果超級好的新型顯示技術嗎?欸,結果最近就真的在車用照明還有中控儀表板那些地方,把可撓式OLED玩出新高度了。
講到這我突然想到,有一次坐朋友新買的車,那個螢幕大得誇張,而且曲線怪漂亮的——但好像扯遠了。拉回來,其實隨著愈來愈多OLED製造商跟汽車品牌合作開發自家專屬應用(就是所謂共同研發),整個技術轉移潮根本加速擴散,於是你看嘛,可撓性顯示器市場一下子膨脹好幾倍也不是什麼奇事。
而且外界現在觀察重點早就從消費電子產品慢慢挪開啦,大概吧,都開始關注智慧座艙、醫療監測還有那種比較冷門的新興工業控制等垂直領域。我自己有時候看到產業新聞也是懷疑,到底是真的趨勢還是炒作啊,但無論怎樣,這現象確實讓供應鏈參與者能去探索更多元化、甚至帶點冒險感的商業可能。有點期待又怕受傷害。
講到這我突然想到,有一次坐朋友新買的車,那個螢幕大得誇張,而且曲線怪漂亮的——但好像扯遠了。拉回來,其實隨著愈來愈多OLED製造商跟汽車品牌合作開發自家專屬應用(就是所謂共同研發),整個技術轉移潮根本加速擴散,於是你看嘛,可撓性顯示器市場一下子膨脹好幾倍也不是什麼奇事。
而且外界現在觀察重點早就從消費電子產品慢慢挪開啦,大概吧,都開始關注智慧座艙、醫療監測還有那種比較冷門的新興工業控制等垂直領域。我自己有時候看到產業新聞也是懷疑,到底是真的趨勢還是炒作啊,但無論怎樣,這現象確實讓供應鏈參與者能去探索更多元化、甚至帶點冒險感的商業可能。有點期待又怕受傷害。

預算有限怎選用?混合方案與拆裝思維大解析
唉,講到這個可撓性OLED啊——資深可靠性工程師老是搖頭嘆氣。沒導入原子層沉積塗層的話,據說通常還沒彎折到一萬次,那失效率就會突然暴衝,欸我自己也覺得有點莫名其妙但數據就是這樣。有人為了流程簡化,直接把那步省掉,可現實常常打臉你,在高溫高濕環境下保存久一點就不太行了,好像很輕鬆結果反而麻煩更多。
其實正確的做法,就是在關鍵製程時段乖乖地加上ALD氧化鋁薄膜沉積啦,雖然工序變繁複、成本也小幅提升,有些人會猶豫,但對產品抗彎能力跟良率的提升真的明顯,你問我值不值得?嗯,大概還是值得吧。有時候寫著寫著就想到,其實這產業裡誰不是邊踩坑邊學。
然後啊,如果彎曲半徑沒有嚴格控管在標準內,比方模組設計時偷懶弄成超過四毫米半徑,看起來方便但問題更大,很容易讓微裂紋慢慢堆積起來,到最後壽命直接縮短。我自己偶爾都會想,是不是大家都心存僥倖呢?總之這兩個陷阱真的不能忽略,不論量產到哪一步,都要記得多留意才好。
其實正確的做法,就是在關鍵製程時段乖乖地加上ALD氧化鋁薄膜沉積啦,雖然工序變繁複、成本也小幅提升,有些人會猶豫,但對產品抗彎能力跟良率的提升真的明顯,你問我值不值得?嗯,大概還是值得吧。有時候寫著寫著就想到,其實這產業裡誰不是邊踩坑邊學。
然後啊,如果彎曲半徑沒有嚴格控管在標準內,比方模組設計時偷懶弄成超過四毫米半徑,看起來方便但問題更大,很容易讓微裂紋慢慢堆積起來,到最後壽命直接縮短。我自己偶爾都會想,是不是大家都心存僥倖呢?總之這兩個陷阱真的不能忽略,不論量產到哪一步,都要記得多留意才好。
輕薄不是萬靈丹,彎折循環背後藏著哪些隱憂
「去年產線那次維修預算超標,原因還不是顯而易見。」採購部的工程師講到柔性OLED後台修復時,語氣裡有點疲憊。唉,柔性薄膜封裝看起來就很輕薄,又標榜密閉性強對吧?但等真的遇到層間破損、甚至掉角什麼的——怎麼說,整個多層阻隔結構都要一層一層拆了再重做,麻煩得讓人頭大。欸,這裡我忽然想起之前有人以為外殼刮痕只是小事,但其實那細縫早已經給水汽找到入口;這種「只要換掉外殼」的想法啊……最後通常成了大坑。嗯,好像現場也常常搞不清楚到底哪裡才是問題根源,有時候拆半天才發現最初的疑點根本誤判。
話說回來,難怪維修費會比傳統玻璃封裝高出數倍。七十多家廠商裡,大多都有被這類隱藏成本拖過後腿吧?這點我是真的聽說不少次。可是早期規劃如果沒把維護費考慮進去,一兩年下來營運預算爆表那也不奇怪,本來講好低成本量產,到最後卻像不停補洞……啊,我又離題了。不過這筆帳其實誰都逃不了,只能各自吞下。好吧,就是這樣。
話說回來,難怪維修費會比傳統玻璃封裝高出數倍。七十多家廠商裡,大多都有被這類隱藏成本拖過後腿吧?這點我是真的聽說不少次。可是早期規劃如果沒把維護費考慮進去,一兩年下來營運預算爆表那也不奇怪,本來講好低成本量產,到最後卻像不停補洞……啊,我又離題了。不過這筆帳其實誰都逃不了,只能各自吞下。好吧,就是這樣。
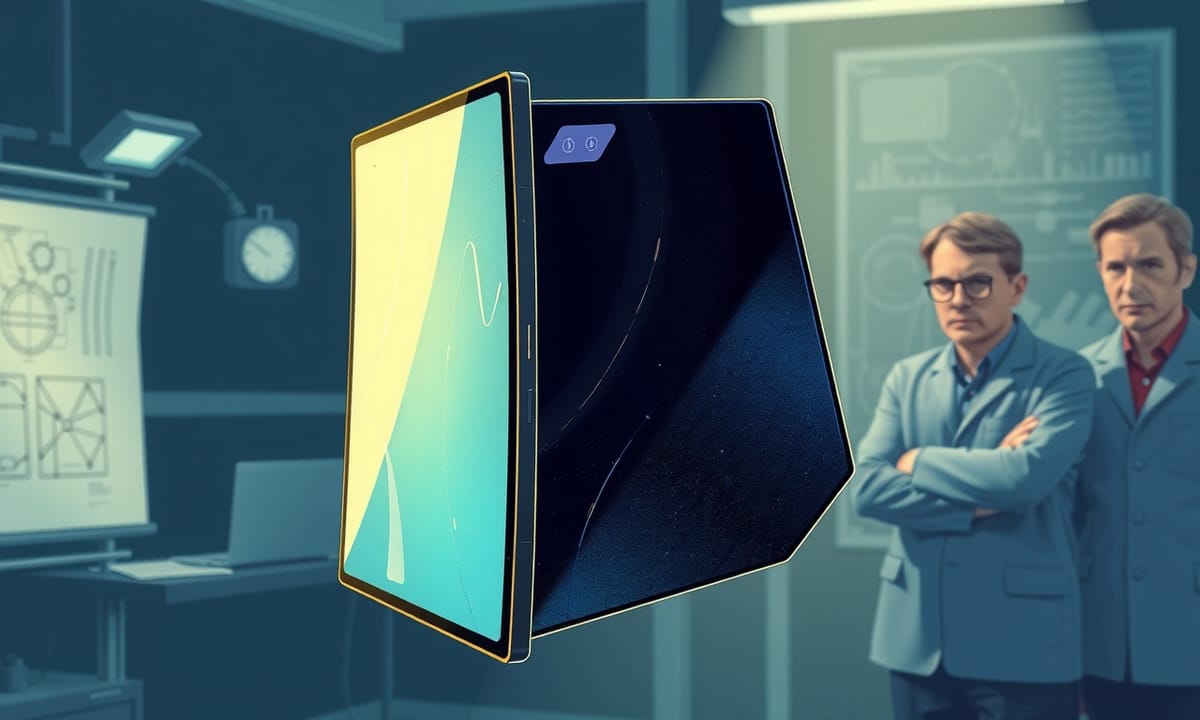
亞洲原料強,美歐封裝策略浮現,垂直市場如何自處
韓國顯示產業協會的二〇二三年報有寫到,柔性OLED這玩意兒,最近在醫療穿戴、車載顯示、智慧型手機、筆記型電腦還有高階家電這五塊領域裡面,慢慢地變得很常見。嗯,有點煩躁,不過還是得繼續講。例如說醫療穿戴,好像將近一半企業都覺得最開始要驗證又要搞合規真的很麻煩,導入時不但得找一堆人去測試,很花錢啦,其實資金壓力也跟著上來。有時候想,他們是不是根本沒辦法負荷啊?嗯…拉回來。
然後車載市場呢,他們卡在那種開車一直震的環境下,需要特別確保可靠度,所以大概三成廠商就是不敢太猛直接換技術,只能一步步來,怕萬一供應鏈斷掉就完蛋了。講到這邊我突然想到前幾天看到有人抱怨供應鏈問題…唉,好像大家的難處都差不多,但還是繼續。
至於智慧型手機和筆記型電腦,你以為需求量超級大就沒事嗎?其實調查裡說有超過七十多家供應商曾經因為材料良率起伏不定,把投產策略整個改掉。真的是無解吧?然後高階家電喔,又受限價格帶,多數只能用混合式封裝設計去分攤成本壓力,不然誰買得起啊?話題岔遠了,我再繞回來。
看現在全球整體狀況,其實企業如果想踏進柔性OLED,一定要結合場域經驗和產線管理能力,不能只靠單純技術升級這麼簡單——這樣才比較能平衡創新風險和長線營運目標,大概如此吧。有時候覺得事情總是比表面複雜。
然後車載市場呢,他們卡在那種開車一直震的環境下,需要特別確保可靠度,所以大概三成廠商就是不敢太猛直接換技術,只能一步步來,怕萬一供應鏈斷掉就完蛋了。講到這邊我突然想到前幾天看到有人抱怨供應鏈問題…唉,好像大家的難處都差不多,但還是繼續。
至於智慧型手機和筆記型電腦,你以為需求量超級大就沒事嗎?其實調查裡說有超過七十多家供應商曾經因為材料良率起伏不定,把投產策略整個改掉。真的是無解吧?然後高階家電喔,又受限價格帶,多數只能用混合式封裝設計去分攤成本壓力,不然誰買得起啊?話題岔遠了,我再繞回來。
看現在全球整體狀況,其實企業如果想踏進柔性OLED,一定要結合場域經驗和產線管理能力,不能只靠單純技術升級這麼簡單——這樣才比較能平衡創新風險和長線營運目標,大概如此吧。有時候覺得事情總是比表面複雜。
引用來源:
- Medical Wearables Market Size, Share, Trends and Revenue ...
Pub.: 2025-01-01 | Upd.: 2025-07-06 - Wearable Medical Devices Market Size | Industry Report 2030
Pub.: 2025-01-12 | Upd.: 2025-06-16 - The Wearable Tech Boom: Key Market Trends, Challenges & Future ...
Pub.: 2025-02-03 | Upd.: 2025-07-21 - [PDF] Development of Wearable Solutions for Healthcare: Initial Stages ...
- Wearable Medical Devices Statistics and Facts (2025)
Pub.: 2025-03-15 | Upd.: 2025-07-20
工藝容差放大效應,材料老化與自動光學檢查的故事
欸,說到韓國顯示產業協會那個什麼…嗯,就是前兩年那組針對可撓性OLED手機做的第三方耐用測試啦,其實你去看,他們只弄了十二週、然後百台樣本在追蹤亮度衰減。這樣真的夠嗎?我自己也懷疑。不知道是不是只有我在意,但他們好像就把那些焦耳熱累積下材料擴散、有機層結晶什麼的都丟一邊耶。
有時候,測試嘛,好像為了省事,反而忽略好多變數——啊,我剛才突然想到昨天外面超熱,然後又下雨,不知道跟OLED有沒有關聯。拉回來講,所以其實不同彎折方式造成的損耗差異,有時可以差到幾倍吧,看資料是這樣寫的。而且只抓單一指標,比如亮度衰減,那根本沒辦法把真實場域裡遇到的各種狀況全都展現出來,有點片面哪。
再說產業資深工程師也蠻直接,他強調如果測試期間沒納進溫度循環跟濕度變化這些條件,其實很容易就低估長期失效率風險。我偶爾會想,是不是大家都太樂觀?唉,也許只是預算問題啦。他建議乾脆監測週期拉長一點,至少半年以上,再配合複雜一點的環境壓力一起考量,才能貼近現實應用情境。不然咧,要不只能自欺欺人了吧。
有時候,測試嘛,好像為了省事,反而忽略好多變數——啊,我剛才突然想到昨天外面超熱,然後又下雨,不知道跟OLED有沒有關聯。拉回來講,所以其實不同彎折方式造成的損耗差異,有時可以差到幾倍吧,看資料是這樣寫的。而且只抓單一指標,比如亮度衰減,那根本沒辦法把真實場域裡遇到的各種狀況全都展現出來,有點片面哪。
再說產業資深工程師也蠻直接,他強調如果測試期間沒納進溫度循環跟濕度變化這些條件,其實很容易就低估長期失效率風險。我偶爾會想,是不是大家都太樂觀?唉,也許只是預算問題啦。他建議乾脆監測週期拉長一點,至少半年以上,再配合複雜一點的環境壓力一起考量,才能貼近現實應用情境。不然咧,要不只能自欺欺人了吧。
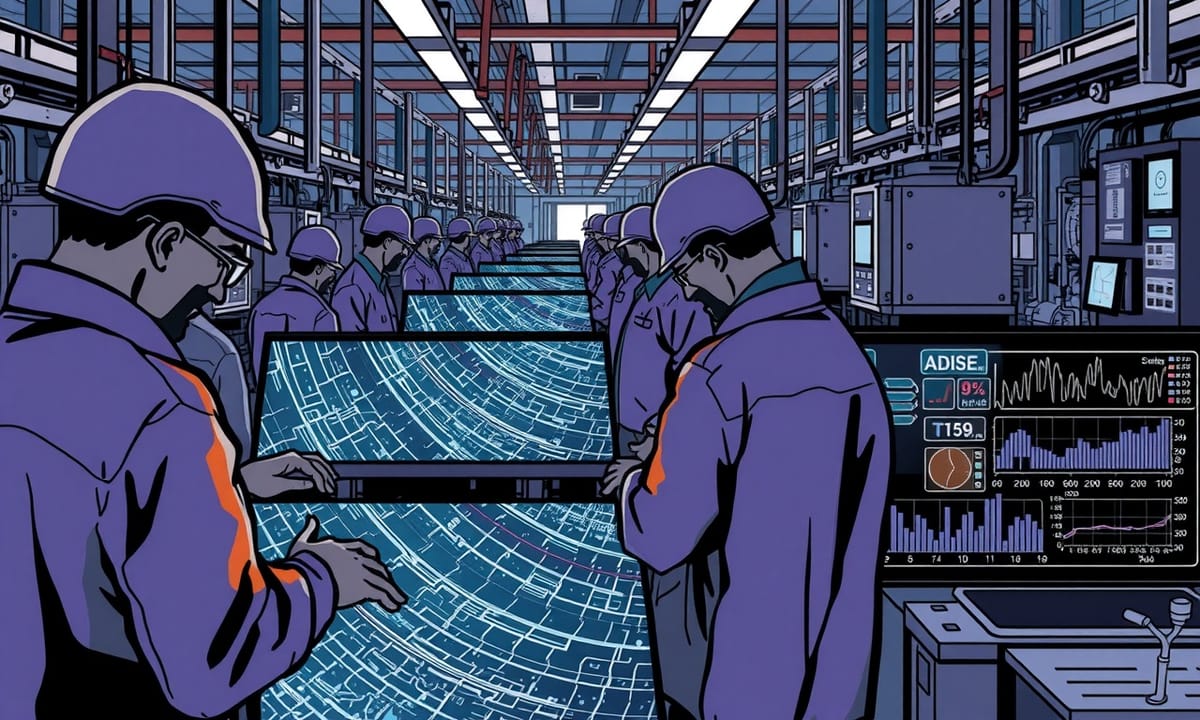
長周期現場亮度追蹤,有效數據怎麼收才有參考性
有些企業剛開始搞可撓性OLED,嗯,老是在單一技術上打轉,或者只是去買現成的材料,完全沒把備援供應鏈這件事放在心上。唉,每次看到這種情況其實挺讓人無奈的。不過話說回來,有時候我自己也會忍不住想,到底是他們太天真還是真的走投無路?拉回正題,其實像這樣忽略備案,很可能導致整批產品推遲上市——尤其你要同時大改基板、封裝什麼的時候,那跨領域協作根本就是場災難。
以前嘛,只靠熟悉的供應商好像還湊合得過去;但新製程現在真的沒辦法了,你得主動規劃多個來源,不然遇到問題就GG,即使前期花費變多、短時間根本回不了本,也是不得不吞下去。欸,我常聽汽車和醫療圈的人抱怨,他們除了要付更高一點的法規認證費,還得掏出將近一半預算做隱性的流程驗證支出(誰叫風險那麼高)。嗯,有時候覺得很煩,但又能怎樣?
如果你的材料供應網絡超級僵硬,一旦某家主要廠商晚交貨或價格亂跳,就只能咬牙延後產品上市──這不是危言聳聽。我突然想到前陣子某間公司被卡半年,他們內部工程師差點抓狂。總之啦,多佈局幾條材料來源,加上備援機制,目前產業界普遍認為是降低上市風險不可或缺的一環吧。好吧,我講完了。
以前嘛,只靠熟悉的供應商好像還湊合得過去;但新製程現在真的沒辦法了,你得主動規劃多個來源,不然遇到問題就GG,即使前期花費變多、短時間根本回不了本,也是不得不吞下去。欸,我常聽汽車和醫療圈的人抱怨,他們除了要付更高一點的法規認證費,還得掏出將近一半預算做隱性的流程驗證支出(誰叫風險那麼高)。嗯,有時候覺得很煩,但又能怎樣?
如果你的材料供應網絡超級僵硬,一旦某家主要廠商晚交貨或價格亂跳,就只能咬牙延後產品上市──這不是危言聳聽。我突然想到前陣子某間公司被卡半年,他們內部工程師差點抓狂。總之啦,多佈局幾條材料來源,加上備援機制,目前產業界普遍認為是降低上市風險不可或缺的一環吧。好吧,我講完了。
規格一改全局變?跨域協同與人才瓶頸難以忽視
「我們前一批在做醫療可撓性OLED顯示模組的時候,嗯,韓國那邊的基材突然斷了——怎麼說呢,這種事總是發生得很突然。」某家台灣系統廠的技術總監有點無奈地提過,他們後來整個案子就因此拖了將近半年。其實光是為了找替代供應商,就耗掉了一個多月時間;你以為像手機或電視那樣,有固定材料商就沒事?唉,偏偏這類客製化需求真的不是單靠一家材料商能撐下去的,所以說,多找幾間備案總是好的,目前我們這產業同行更喜歡有能力水平或垂直整合的供應商: 像 WiseChip(智晶光電)或曜凌光電這種專攻 PMOLED 技術的亞洲廠商,更擅長客製特定解決方案 — 比方醫療儀器、工業顯示、穿戴設備等等。
欸,我想起來,上次有人還說日本供應鏈對於生物相容性的要求特別嚴格,每次審核流程都慢得讓人抓狂…好啦,不扯遠,其實不只他們,有些業者乾脆直接先導入大約三成左右現地採購配套,把那些基本料件切分成幾組,各自找不同來源分散風險。雖然表面看起來複雜到頭痛,但據他們自己講,好像真的可以大幅減少延誤機率吧。
我本來以為只有老行家才會拆規格,但有些新進工業用戶也沒太排斥把PMOLED各項規格細拆,只是測試週期啊……肯定要拉長不少。有趣的是,西方那些平台型公司,大多還是習慣一次談定比較大範圍協作——這樣彼此間預期常常錯開很多拍,到底哪種模式比較適合?唔,看領域,也看雙方合作熟度囉。
欸,我想起來,上次有人還說日本供應鏈對於生物相容性的要求特別嚴格,每次審核流程都慢得讓人抓狂…好啦,不扯遠,其實不只他們,有些業者乾脆直接先導入大約三成左右現地採購配套,把那些基本料件切分成幾組,各自找不同來源分散風險。雖然表面看起來複雜到頭痛,但據他們自己講,好像真的可以大幅減少延誤機率吧。
我本來以為只有老行家才會拆規格,但有些新進工業用戶也沒太排斥把PMOLED各項規格細拆,只是測試週期啊……肯定要拉長不少。有趣的是,西方那些平台型公司,大多還是習慣一次談定比較大範圍協作——這樣彼此間預期常常錯開很多拍,到底哪種模式比較適合?唔,看領域,也看雙方合作熟度囉。
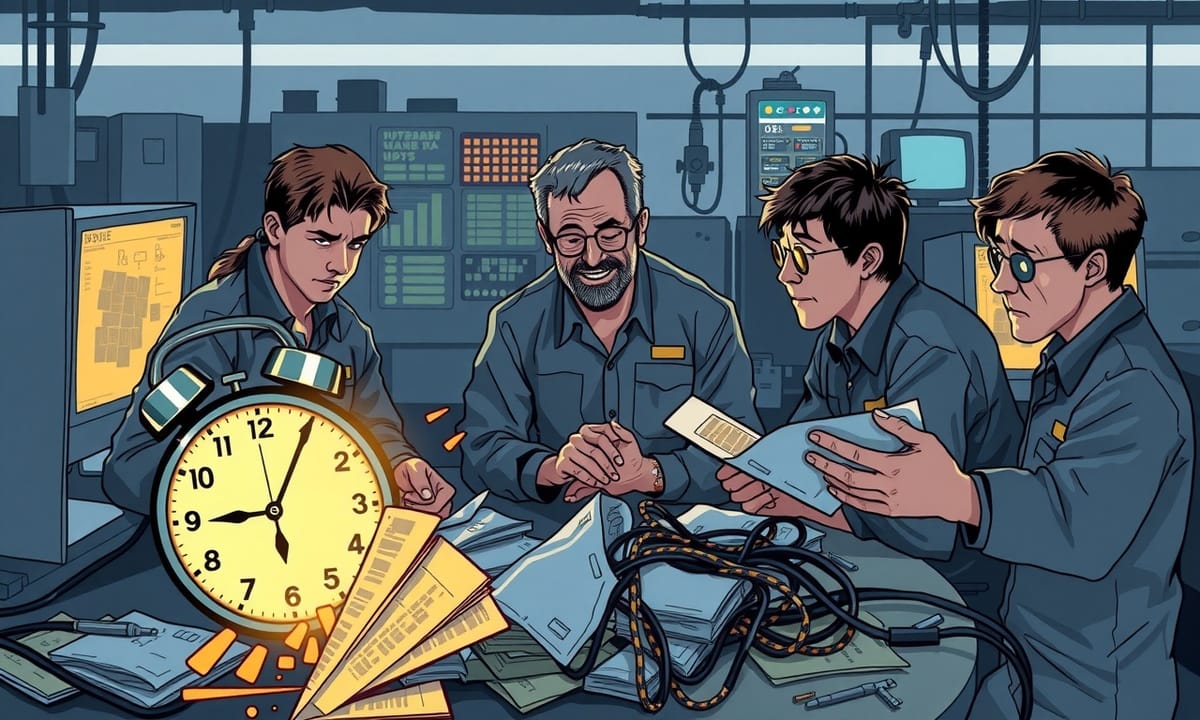
外型很美但易壞?總成本、維護門檻才是真功夫
過去大家都一直在講什麼柔性基板的可撓性,總覺得要越軟越好,對吧?可是,嗯……最近翻了一下歐洲OLED產業論壇那些厚厚的會議紀錄——唉,其實也不是很想看啦,但還是硬著頭皮讀完了——發現業界好像開始懷疑:真的有必要追求極致柔性嗎?這話是某位材料科學專家說的,我也沒見過他本人。
然後,他進一步提到,roll-to-roll製程跟柔性基板結合確實讓成本結構有點變化,好像競爭重點已經從以前大家搶設備資本那一塊,慢慢轉到材料本身還有製程技術上。不過,我突然想到上次某家廠商老闆說午餐難吃……呃,不重要。拉回來,其實當新技術用到智慧紡織品、穿戴醫療裝置時,你以為最難的是彎折半徑嗎?結果,不少企業反映說OLED壽命跟系統整合才真的是惱人得不得了。
還有一個日系廠的工程主管,他自己倒覺得適度彈性比較實際吧——因為這樣模組形變比較能控制,而且維持光學穩定也省事多了。就驗證週期來說,也不用拖超久才搞定(這講起來輕鬆,其實每次驗證都讓人快爆炸)。唉,有時候追求最大柔度根本沒啥好處,反而測試程序一拉長、可靠度提升不上去,整個團隊心情都受影響。他們蠻認真強調,如果只盲目追高極限,一不小心反而掉進坑裡爬不出來。
所以啊,那些準備加入競爭的新手們,被提醒一句:材料選型還有應用場景真的要綁緊一些思考,大概只有這樣才能在新局面裡摸索到突破口吧。我也是邊寫邊懷疑,到底自己是不是理解全部重點……但先就這樣吧。
然後,他進一步提到,roll-to-roll製程跟柔性基板結合確實讓成本結構有點變化,好像競爭重點已經從以前大家搶設備資本那一塊,慢慢轉到材料本身還有製程技術上。不過,我突然想到上次某家廠商老闆說午餐難吃……呃,不重要。拉回來,其實當新技術用到智慧紡織品、穿戴醫療裝置時,你以為最難的是彎折半徑嗎?結果,不少企業反映說OLED壽命跟系統整合才真的是惱人得不得了。
還有一個日系廠的工程主管,他自己倒覺得適度彈性比較實際吧——因為這樣模組形變比較能控制,而且維持光學穩定也省事多了。就驗證週期來說,也不用拖超久才搞定(這講起來輕鬆,其實每次驗證都讓人快爆炸)。唉,有時候追求最大柔度根本沒啥好處,反而測試程序一拉長、可靠度提升不上去,整個團隊心情都受影響。他們蠻認真強調,如果只盲目追高極限,一不小心反而掉進坑裡爬不出來。
所以啊,那些準備加入競爭的新手們,被提醒一句:材料選型還有應用場景真的要綁緊一些思考,大概只有這樣才能在新局面裡摸索到突破口吧。我也是邊寫邊懷疑,到底自己是不是理解全部重點……但先就這樣吧。
極致封裝厚度vs維修友善:設計初衷該往哪裡站
嗯,說到醫療、汽車或工業那些應用場景裡的可撓性OLED產品,其實啊,還是得先好好想清楚現場到底需要什麼,不然瞎忙一通也只是白費力氣。關鍵性能指標這東西,真的是每個場合都不太一樣,有時候會覺得怎麼老是在調規格,好煩,但還是必須硬著頭皮界定清楚才行。然後可靠性門檻——唉,就是那種「不能壞」的標準啦,你說誰願意買個一直故障的東西呢?有點離題了,我拉回來。
執行階段嘛,通常要一步步去看,比如供應鏈有沒有備援能力,如果遇到突發狀況是不是馬上就斷貨了?想到這裡忍不住又想起之前某次材料缺貨搞得大家焦頭爛額……算了,不提那些鳥事,多層封裝維修成本也是要列進評估表單裡面,不然最後帳單攤開很容易傻眼。再加上材料驗證週期,有時候廠商愛拖,一等就是好幾週,真的挺磨人的。不過建立多元技術合作管道蠻重要的啦,大概可以分散些風險,也比較能互補短板。
方案選擇那邊,要特別小心那種只顧追新、結果忽略掉後續維護和一些藏在細節裡面的支出。有時候看到亮眼新技術會心癢癢,但冷靜想想,以後營運預算爆表就麻煩了。對了,測試樣本數量和環境條件也不能隨便敷衍,要認真規劃一下,不然萬一漏掉什麼情境,到時候問題爆出來也是自己收拾。
設計流程中,其實採漸進式轉換策略比較穩妥吧——突然切換供應商誰都怕原本搭好的關係全毀,那種尷尬局面我光想就頭痛。欸,我剛剛是不是講偏了?總之,再找垂直領域整合能力強的夥伴來協作,跨學科挑戰不是嘴上說說那麼簡單,有人一起扛壓力才走得久。差不多,就醬子吧。
執行階段嘛,通常要一步步去看,比如供應鏈有沒有備援能力,如果遇到突發狀況是不是馬上就斷貨了?想到這裡忍不住又想起之前某次材料缺貨搞得大家焦頭爛額……算了,不提那些鳥事,多層封裝維修成本也是要列進評估表單裡面,不然最後帳單攤開很容易傻眼。再加上材料驗證週期,有時候廠商愛拖,一等就是好幾週,真的挺磨人的。不過建立多元技術合作管道蠻重要的啦,大概可以分散些風險,也比較能互補短板。
方案選擇那邊,要特別小心那種只顧追新、結果忽略掉後續維護和一些藏在細節裡面的支出。有時候看到亮眼新技術會心癢癢,但冷靜想想,以後營運預算爆表就麻煩了。對了,測試樣本數量和環境條件也不能隨便敷衍,要認真規劃一下,不然萬一漏掉什麼情境,到時候問題爆出來也是自己收拾。
設計流程中,其實採漸進式轉換策略比較穩妥吧——突然切換供應商誰都怕原本搭好的關係全毀,那種尷尬局面我光想就頭痛。欸,我剛剛是不是講偏了?總之,再找垂直領域整合能力強的夥伴來協作,跨學科挑戰不是嘴上說說那麼簡單,有人一起扛壓力才走得久。差不多,就醬子吧。
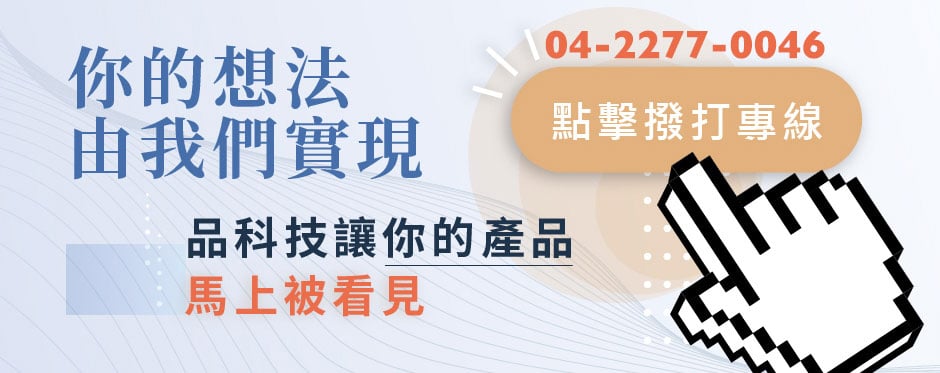